Are American Workers Ready For The Reshoring Of Manufacturing Jobs?
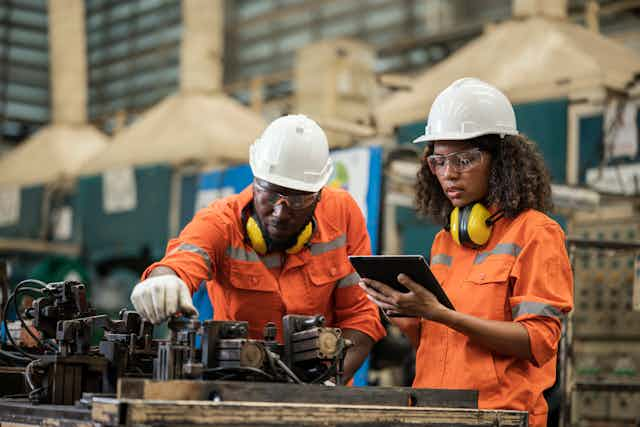
Table of Contents
The Skills Gap: A Major Hurdle to Reshoring Success
A significant disparity exists between the skills required for modern manufacturing jobs and the skills possessed by the current American workforce. This skills gap represents a major hurdle to the successful reshoring of manufacturing jobs. The demand for skilled labor far outstrips the supply, creating a bottleneck for companies looking to expand domestic production. This shortage is particularly acute in specific manufacturing sectors.
- Shortage of skilled machinists, welders, and robotic technicians: Many existing facilities lack the skilled labor needed to operate advanced machinery and implement new technologies.
- Lack of advanced digital skills (e.g., programming, data analysis): Modern manufacturing relies heavily on data-driven decision making and sophisticated automation systems, requiring workers with advanced digital literacy.
- Need for improved problem-solving and critical thinking abilities: Troubleshooting complex equipment and adapting to evolving production processes demand strong analytical and problem-solving skills.
- Growing demand for workers with experience in automation and robotics: The increasing integration of robots and automated systems necessitates a workforce proficient in operating, maintaining, and programming these technologies.
Statistics highlight the severity of this issue. For example, a recent report by [Insert credible source and statistic here] indicates a projected shortage of [Number] skilled manufacturing workers by [Year]. Addressing this skills gap is paramount to ensuring a successful manufacturing resurgence.
Workforce Development Initiatives: Bridging the Skills Gap
Numerous workforce development initiatives are underway to bridge the skills gap and prepare American workers for reshored manufacturing jobs. These initiatives encompass a range of programs designed to upskill and retrain individuals, equipping them with the necessary competencies for success in the modern manufacturing environment.
- Government-funded apprenticeship programs: These programs offer structured on-the-job training combined with classroom instruction, providing a pathway to skilled trades.
- Community college partnerships with manufacturing companies: Many community colleges collaborate with manufacturers to develop curriculum tailored to industry needs, ensuring graduates possess relevant skills.
- Private sector initiatives offering training and development opportunities: Companies are increasingly investing in their own training programs to upskill existing employees and attract new talent.
- Effectiveness of online and on-the-job training programs: While online learning offers flexibility and accessibility, on-the-job training provides hands-on experience crucial for many manufacturing roles. The effectiveness of these programs varies, depending on factors such as quality of instruction and integration with real-world applications.
The success of these initiatives depends on effective collaboration between government agencies, educational institutions, and the private sector, ensuring alignment between training programs and industry demands.
The Impact of Automation and Technological Advancements
Automation and technological advancements are fundamentally reshaping the manufacturing landscape. While some fear widespread job displacement, the reality is more nuanced. While automation will undoubtedly eliminate some lower-skilled jobs, it also creates new opportunities for higher-skilled workers. The adoption of Industry 4.0 technologies, including robotics, AI, and smart manufacturing systems, necessitates a workforce capable of managing, maintaining, and innovating within these advanced systems.
- Increased reliance on robotics and automation in factories: Automation improves efficiency, precision, and productivity, but also requires skilled technicians to operate and maintain these systems.
- The emergence of new roles requiring expertise in automation technologies: Jobs such as robotics engineers, data analysts, and automation technicians are in high demand.
- The need for workers to adapt to a rapidly changing technological environment: Continuous learning and upskilling are crucial for workers to remain relevant in a technologically evolving sector.
- The importance of reskilling initiatives to prepare workers for automation-related roles: Investing in reskilling programs focused on automation technologies will be essential to ensure a smooth transition for existing workers.
The successful integration of automation requires a proactive approach to workforce development, focusing on equipping workers with the skills to thrive in this new environment.
Attracting and Retaining Talent in the Reshoring Era
Attracting and retaining skilled workers is crucial for the success of reshoring initiatives. In a competitive job market, manufacturers must offer compelling employment packages and cultivate a positive work environment.
- Competitive wages and benefits packages to attract top talent: Offering salaries and benefits that are comparable to, or better than, those in other industries is essential.
- Creating a positive work environment and fostering a strong company culture: A positive work environment, with opportunities for growth and development, significantly impacts employee satisfaction and retention.
- Investing in employee development and career advancement opportunities: Providing ongoing training and development opportunities demonstrates a commitment to employees’ growth and increases their loyalty.
- Improving work-life balance to increase employee satisfaction: Offering flexible work arrangements and prioritizing employee well-being can improve employee satisfaction and reduce turnover.
Conclusion
The reshoring of manufacturing jobs presents a significant opportunity for the US economy, but realizing this potential requires a concerted effort to address the skills gap and prepare the American workforce. While automation will transform the manufacturing landscape, it will also create new, higher-skilled jobs. Investing in workforce development programs, including apprenticeships, vocational training, and reskilling initiatives, is crucial for ensuring American workers are equipped to fill these roles. Furthermore, companies must focus on attracting and retaining talent by offering competitive wages, benefits, and a positive work environment. Investing in workforce development programs is crucial for ensuring American workers are ready for the reshoring of manufacturing jobs. Learn more about available training programs and how you can contribute to the future of American manufacturing.
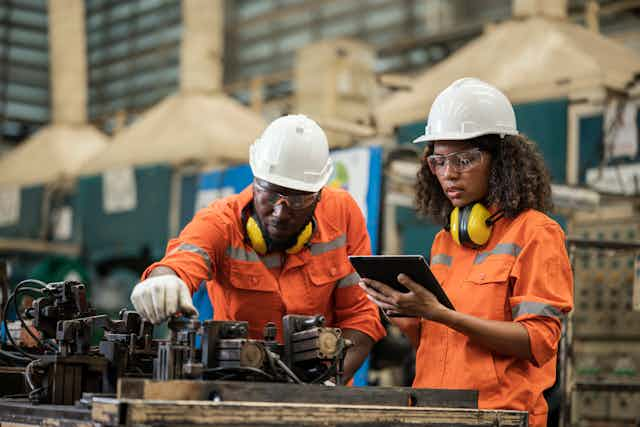
Featured Posts
-
Vybz Kartel Announces New York City Barclay Center Concert
May 21, 2025 -
Burkardt And Amiri Power Mainz To Victory Against Rb Leipzig
May 21, 2025 -
Reducing Trade Barriers Switzerland And Chinas Dialogue On Tariffs
May 21, 2025 -
Navy Officer Burke Accused Of Bribery In Job Swap Scheme
May 21, 2025 -
Manchester Citys Next Manager Could An Arsenal Legend Replace Guardiola
May 21, 2025
Latest Posts
-
Rb Leipzig Fall To Mainz Burkardt And Amiris Decisive Contributions
May 21, 2025 -
Gladbach Defeat Mainzs Top Four Bid Strengthened
May 21, 2025 -
Mainz Overcome Leipzig Burkardt And Amiri Lead The Charge
May 21, 2025 -
Burkardt And Amiri Power Mainz To Victory Against Rb Leipzig
May 21, 2025 -
Staying Safe During Storms With High Winds
May 21, 2025