Automated Visual Inspection Of Lyophilized Vials: Challenges And Solutions
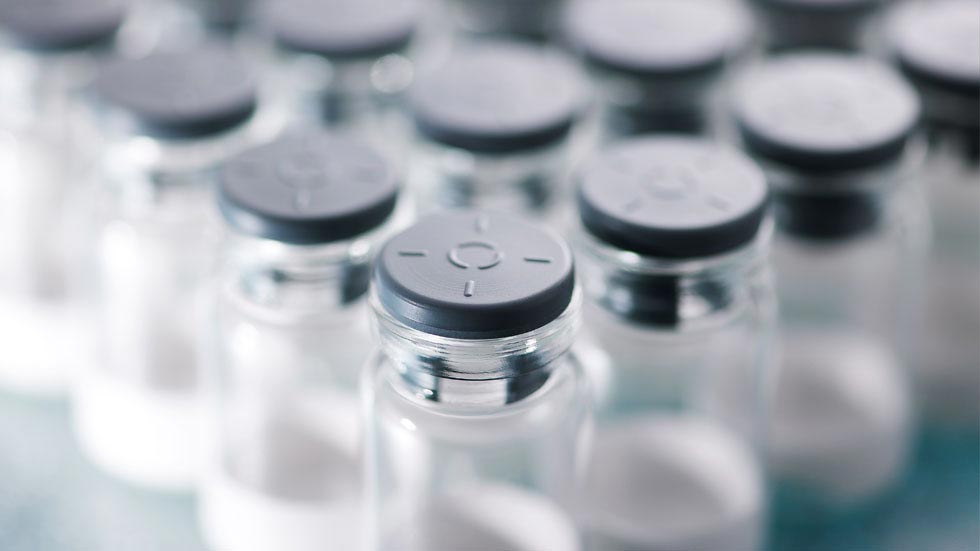
Table of Contents
Challenges in Manual Visual Inspection of Lyophilized Vials
Manual visual inspection of lyophilized vials presents several significant hurdles that impact quality, efficiency, and ultimately, profitability.
Subjective Interpretation and Variability
Human inspectors, despite their training, face inherent limitations. Fatigue, varying interpretations of defects, and inconsistencies in lighting and viewing angles all contribute to subjective results.
- Examples of subjective defects: Slight discoloration, subtle particulate matter, minor cracks in the vial, inconsistencies in the lyophilized cake.
- Consequences of human error: Overlooking critical defects, inconsistent rejection rates leading to batch variability, increased risk of releasing sub-standard products. This can result in costly recalls and reputational damage.
Bottlenecks and Low Throughput
Manual inspection is a significant bottleneck in high-volume pharmaceutical manufacturing. The slow, labor-intensive nature of the process dramatically impacts production speed and lead times.
- Increased labor costs: Manual inspection requires significant staffing, increasing operational expenses.
- Difficulty in scaling up production: Manual methods struggle to adapt to increased production demands, hindering growth and expansion. Scaling up requires a disproportionate increase in personnel and time.
Maintaining Sterility and Contamination Risk
Manual handling of vials introduces a risk of contamination, jeopardizing the sterility of the product.
- Risk of introducing particulates: Human handling increases the chance of introducing foreign particles into the vials during the inspection process.
- Difficulties in maintaining a sterile environment: Maintaining a sterile environment during manual inspection is challenging, increasing the risk of contamination and product spoilage.
Advantages of Automated Visual Inspection Systems
Automated visual inspection systems offer compelling advantages over manual methods, addressing many of the aforementioned challenges.
Improved Accuracy and Consistency
Automated systems provide objective and consistent inspection results, eliminating the subjectivity inherent in manual inspection.
- Reduced false positives and false negatives: Advanced algorithms ensure accurate defect detection, minimizing errors.
- Consistent defect detection across different batches and operators: Automated systems provide uniform inspection standards regardless of who is operating them or the time of day.
Increased Throughput and Efficiency
Automated systems dramatically increase inspection speed and efficiency, processing significantly more vials per hour than manual methods.
- Faster processing of large volumes of vials: Automated systems can handle high-throughput requirements, meeting the demands of large-scale manufacturing.
- Reduced labor costs and improved production efficiency: Automation reduces reliance on manual labor, leading to significant cost savings and enhanced productivity.
Enhanced Data Management and Traceability
Automated systems generate detailed reports, track defects, and ensure complete traceability, improving compliance and quality control.
- Real-time monitoring and data analysis: Automated systems provide real-time data on defect rates, enabling proactive adjustments to the manufacturing process.
- Improved compliance with regulatory requirements: Detailed data logging and traceability features meet the stringent documentation needs of regulatory bodies (e.g., FDA, EMA).
Minimizing Contamination Risk
Automated systems minimize human contact, reducing the risk of particulate contamination and ensuring a sterile environment.
- Reduced risk of particulate contamination: Automated systems minimize human intervention, significantly lowering the risk of introducing contaminants.
- Improved overall product quality and safety: By minimizing contamination risks, automated inspection improves overall product quality and enhances patient safety.
Selecting the Right Automated Visual Inspection System
Choosing the right automated system requires careful consideration of several factors.
Key Considerations for System Selection
The ideal system depends on specific needs and production parameters.
- Different technologies used in automated visual inspection: Machine vision systems using advanced image analysis techniques, AI-powered defect detection algorithms, and other technologies provide varying capabilities.
- Throughput requirements: The system should meet the required production volume and speed. Consider the number of vials processed per hour.
- Vial size and shape: The system should be compatible with the specific dimensions and type of vials used in your process.
- Types of defects to be detected: The system should be capable of identifying the specific defects relevant to your products.
- Budget constraints: Evaluate the initial investment cost and long-term maintenance expenses.
- Integration with existing production lines: Seamless integration into existing manufacturing workflows is crucial for optimal efficiency.
Validation and Regulatory Compliance
Validation and regulatory compliance are critical aspects of implementing an automated visual inspection system.
- Documentation requirements for automated visual inspection systems: Detailed documentation is essential for demonstrating compliance with regulatory requirements (e.g., GMP, 21 CFR Part 11).
- Qualification and validation protocols: Rigorous qualification and validation procedures are necessary to ensure system accuracy and reliability.
Conclusion
Manual visual inspection of lyophilized vials presents significant challenges related to accuracy, efficiency, and sterility. Automated visual inspection systems offer a compelling solution, providing improved accuracy, increased throughput, enhanced data management, and reduced contamination risk. Selecting the appropriate system requires careful consideration of factors such as throughput, vial type, defect types, and regulatory requirements. Investing in automated visual inspection of lyophilized vials is crucial for modern pharmaceutical manufacturing. Contact us today to explore how our automated solutions can improve your quality control and increase your production efficiency.
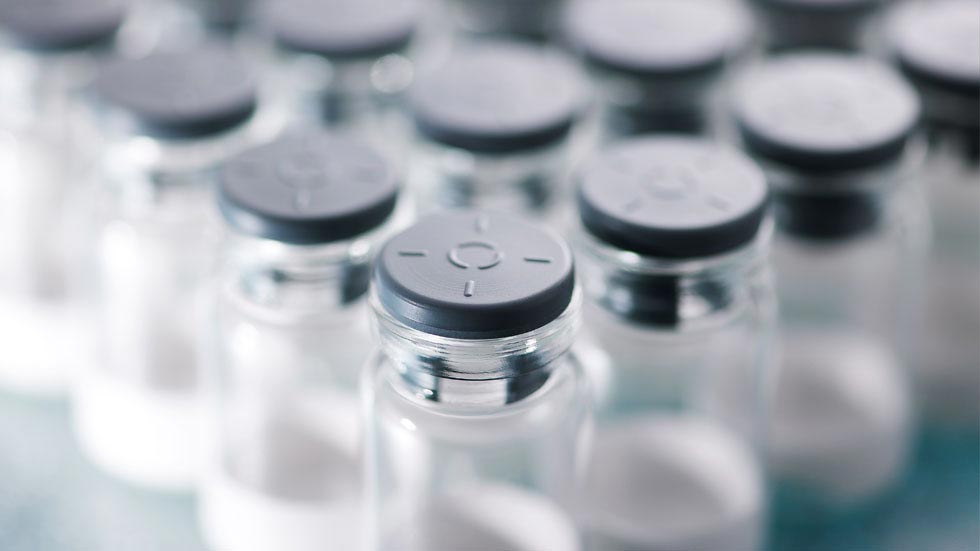
Featured Posts
-
Cassidy Hutchinson January 6th Hearing Witness To Publish Memoir This Fall
May 11, 2025 -
After Pope Francis 9 Potential Successors And The Future Of The Catholic Church
May 11, 2025 -
Unlocking Maximum Profits The Simplicity Of High Yield Dividend Investing
May 11, 2025 -
New Mom Lily Collins Stunning Calvin Klein Ads Image 5133598
May 11, 2025 -
Spotlight On Rotorua Discovering New Zealands Cultural Heartbeat
May 11, 2025