Cost-Cutting Measures Surge In U.S. Due To Tariff Instability
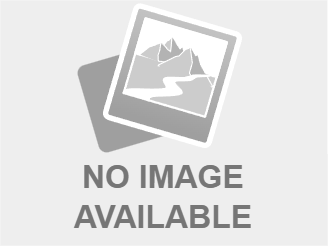
Table of Contents
Impact of Tariffs on Business Costs
Tariff instability significantly impacts business costs in several ways, creating a ripple effect throughout the economy. The increased uncertainty makes long-term planning difficult and forces businesses to prioritize short-term survival.
Increased Raw Material Prices
Tariffs directly inflate the cost of imported raw materials, a critical component for many US businesses. This price increase squeezes profit margins and forces businesses to seek cost reductions elsewhere.
- Manufacturing: The automotive industry, for example, faces higher costs for steel and aluminum, leading to increased vehicle prices and reduced competitiveness.
- Agriculture: Farmers reliant on imported fertilizers and machinery experience higher input costs, impacting their profitability and potentially food prices for consumers.
- Technology: The electronics industry faces higher costs for components like semiconductors and rare earth minerals, impacting the pricing and availability of consumer electronics.
A recent study by the [Insert credible source, e.g., Brookings Institution] estimated that tariffs have increased the cost of raw materials by an average of [Insert percentage or statistic]%, significantly impacting profitability across various sectors.
Supply Chain Disruptions
Tariff uncertainty creates significant supply chain disruptions, adding another layer of cost to businesses. The unpredictable nature of tariffs makes it difficult to forecast demand and manage inventory effectively.
- Forecasting Challenges: Businesses struggle to accurately predict future demand due to the shifting landscape of import costs. This leads to overstocking or understocking, both of which increase costs.
- Increased Transportation Costs: Businesses may need to reroute shipments to avoid tariffs, leading to increased transportation costs and delivery times.
- Inventory Management: The uncertainty makes it challenging to optimize inventory levels, leading to potential storage costs and risks of obsolescence.
Companies are employing various strategies to mitigate supply chain disruptions, including diversifying suppliers, building stronger relationships with key suppliers, and investing in inventory management technology.
Strategies for Cost Reduction
Faced with increased costs and economic uncertainty, US businesses are adopting various cost-cutting strategies, often impacting employees and operations significantly.
Labor Cost Reductions
Many businesses are resorting to labor cost reductions to maintain profitability in the face of tariff instability. This can manifest in several ways:
- Layoffs: Companies are reducing their workforce to cut payroll expenses, a drastic measure with significant social and economic consequences.
- Wage Freezes: Freezing or limiting wage increases prevents labor costs from rising, but can negatively impact employee morale and productivity.
- Reduced Benefits: Cutting employee benefits, such as health insurance or retirement contributions, is another common cost-cutting measure. However, this can also impact employee retention and attract less talent. Legal considerations are critical to ensure compliance with employment laws.
These measures, while necessary for survival for some, can have long-term negative impacts on employee morale, productivity, and the overall business environment.
Automation and Technology Adoption
To increase efficiency and reduce reliance on labor, businesses are increasingly investing in automation and technology.
- Robotics: Implementing robots in manufacturing and warehousing reduces labor costs and improves productivity.
- AI-powered systems: Utilizing AI for tasks such as inventory management, customer service, and data analysis streamlines operations and reduces the need for human resources.
- Software solutions: Implementing specialized software for various business functions improves efficiency and automates tasks.
While the initial investment in automation and technology can be substantial, the long-term cost savings can outweigh the initial expense, particularly in light of rising labor costs and tariff-related pressures. However, this often leads to job displacement that needs to be carefully addressed.
Reshoring and Nearshoring
To mitigate tariff-related costs and increase supply chain resilience, many companies are exploring reshoring (bringing production back to the US) and nearshoring (moving production to nearby countries).
- Reduced Transportation Costs: Bringing production closer to home reduces transportation costs and lead times.
- Increased Control: Businesses gain greater control over their supply chains and quality control.
- Potential Job Creation: Reshoring and nearshoring can create domestic jobs, but it may also increase production costs compared to overseas manufacturing.
However, reshoring and nearshoring also present challenges, including higher labor costs and potential difficulties in finding suitable infrastructure and skilled labor domestically.
Government Policies and Their Role
Government policies play a crucial role in shaping the response of businesses to tariff instability.
Government Support Programs
The government offers various support programs aimed at helping businesses cope with the challenges of tariff instability. These include:
- Loans and grants: Several programs offer financial assistance to businesses affected by tariffs.
- Tax incentives: Tax breaks and credits can incentivize businesses to invest in domestic production and reduce reliance on imports.
- Trade adjustment assistance: Programs like the Trade Adjustment Assistance (TAA) program provide assistance to workers displaced by trade.
Businesses should thoroughly research available government support programs to access potential relief.
Policy Uncertainty and its Effects
Uncertainty surrounding future tariff policies significantly discourages investment and hinders long-term planning.
- Reduced Business Confidence: Unpredictable tariffs erode business confidence, making businesses hesitant to invest in expansion or new projects.
- Impact on Investment Decisions: Uncertainty makes it difficult for businesses to make informed investment decisions, hindering long-term growth.
- Overall Economic Growth: The lack of investment and business uncertainty negatively impact overall economic growth.
Conclusion
Tariff instability has profoundly impacted US businesses, leading to a surge in cost-cutting measures. Increased raw material prices, supply chain disruptions, and overall economic uncertainty have forced companies to implement various strategies, ranging from labor cost reductions to automation and reshoring. Understanding the full impact of cost-cutting measures requires a comprehensive analysis of tariff instability. Explore these issues further by reviewing relevant government reports and industry analyses to better understand and mitigate tariff instability's impact on your business and develop effective cost-cutting strategies.
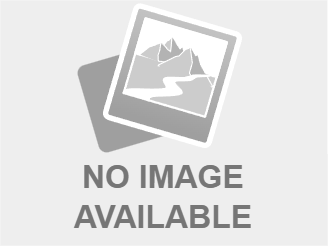
Featured Posts
-
Blue Origin Rocket Launch Cancelled Vehicle Subsystem Issue
Apr 29, 2025 -
From Waste To Words An Ai Solution For Transforming Repetitive Scatological Documents Into Podcasts
Apr 29, 2025 -
Debate Surrounding Convicted Cardinals Vote In Upcoming Conclave
Apr 29, 2025 -
Double Strike Cripples Hollywood What It Means For Film And Television
Apr 29, 2025 -
Securing Your Capital Summertime Ball 2025 Tickets
Apr 29, 2025