Improving Automated Visual Inspection For Lyophilized Vials: A Practical Guide
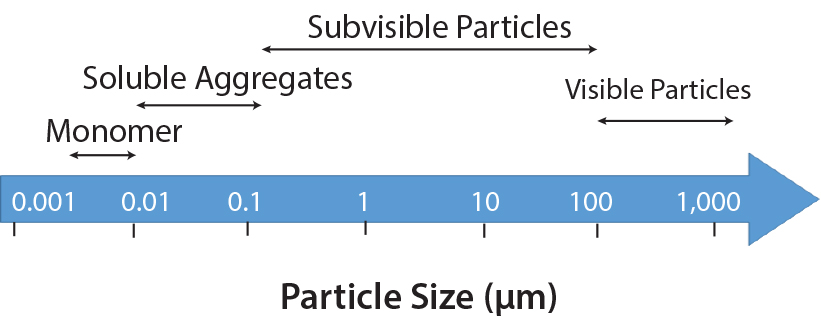
Table of Contents
Selecting the Right Automated Visual Inspection System
Choosing the right automated system is crucial for effective lyophilized vial inspection. The selection process must consider several key factors, including system capabilities, validation requirements, and cost-benefit analysis.
Understanding System Capabilities
Modern automated visual inspection systems leverage advanced technologies like machine vision and sophisticated image processing algorithms to detect a wide range of defects in lyophilized vials. These defects include:
- Cracks in the vial glass
- Particulate matter within the vial
- Discoloration or inconsistencies in the lyophilized cake
- Improper stopper placement or seating
- Vial labeling defects
When selecting a system, consider these essential features:
- High-resolution cameras: Ensuring clear visualization of even minute defects.
- Versatile lighting options: Including coaxial, diffuse, and backlighting for optimal contrast and defect visibility.
- High throughput: Processing a large number of vials per hour to meet production demands.
- Easy integration: Seamless integration with existing production lines and data management systems.
- Advanced algorithms: Capable of detecting subtle defects and minimizing false positives/negatives.
Validation and Qualification
Regulatory compliance, particularly adherence to standards like 21 CFR Part 11, is paramount. Thorough validation and qualification are essential to ensure the system's reliability and accuracy. This process typically involves:
- Installation Qualification (IQ): Verification that the system is installed according to specifications.
- Operational Qualification (OQ): Confirmation that the system operates within predefined parameters.
- Performance Qualification (PQ): Demonstration that the system consistently meets performance requirements.
- Data integrity: Ensuring the accuracy, completeness, and reliability of inspection data.
- Traceability: Maintaining a complete audit trail of all system activities.
Cost-Benefit Analysis
Implementing an automated visual inspection system involves an initial investment, but the long-term benefits significantly outweigh the costs. Consider these factors in your cost-benefit analysis:
- Reduced labor costs: Automation significantly reduces the need for manual inspection personnel.
- Improved product quality: Minimizing defective products reaching the market.
- Increased throughput: Faster inspection speeds leading to higher production efficiency.
- Reduced product waste: Fewer rejected vials due to improved accuracy.
- Enhanced regulatory compliance: Meeting stringent quality and documentation requirements.
Optimizing the Inspection Process for Lyophilized Vials
Optimizing the inspection process involves carefully managing image acquisition, leveraging appropriate defect detection algorithms, and effectively analyzing the generated data.
Image Acquisition and Preprocessing
High-quality images are critical for accurate defect detection. Optimize image acquisition by:
- Careful lighting selection: Different lighting techniques (diffuse, coaxial) highlight different types of defects.
- Precise camera angle and focus: Ensuring consistent and clear images.
- Image preprocessing: Techniques like noise reduction and contrast enhancement improve defect visibility.
Defect Detection Algorithms
The selection of appropriate defect detection algorithms is crucial. Consider using:
- Template matching: Useful for detecting known defects with well-defined characteristics.
- Machine learning algorithms: Adaptable and capable of learning and identifying a wider range of defects, even subtle variations.
Data Analysis and Reporting
Effective data analysis is essential for process improvement and regulatory compliance:
- Data visualization: Creating clear and concise reports to monitor inspection results.
- Trend analysis: Identifying patterns and potential issues over time.
- Statistical Process Control (SPC): Implementing statistical methods to monitor process stability and identify deviations.
Addressing Challenges in Automated Visual Inspection of Lyophilized Vials
Even with advanced systems, challenges can arise. Addressing these effectively is critical for successful implementation.
Handling Variability in Lyophilization
Lyophilization processes can produce variations in vial fill levels, cake appearance, and stopper placement. Mitigate these challenges through:
- Advanced image segmentation: Precisely isolating the areas of interest within the vial image.
- Adaptive thresholding: Adjusting the sensitivity of the defect detection algorithms based on the variability observed.
Dealing with False Positives and Negatives
Minimizing false positives (rejecting good vials) and false negatives (accepting defective vials) is crucial for accuracy:
- Algorithm retraining: Improving algorithm performance by retraining with a larger and more diverse dataset.
- Adjusting inspection parameters: Fine-tuning the sensitivity and specificity of the system.
Maintaining System Performance
Consistent performance requires regular maintenance and training:
- Preventive maintenance: Following a scheduled maintenance program to prevent unexpected downtime.
- Regular calibration: Ensuring the system's accuracy and precision.
- Operator training: Providing comprehensive training to operators on system operation and maintenance.
Conclusion
Implementing automated visual inspection for lyophilized vials offers significant advantages, including increased efficiency, improved accuracy, reduced labor costs, and enhanced regulatory compliance. By carefully selecting the right system, optimizing the inspection process, and proactively addressing potential challenges, pharmaceutical manufacturers can significantly improve their quality control and ensure the delivery of safe and effective products. Invest in advanced automated visual inspection solutions today to elevate your lyophilized vial inspection process and ensure the highest quality standards. Contact a leading supplier of automated visual inspection systems to learn more about improving automated visual inspection for lyophilized vials and find the perfect solution for your needs.
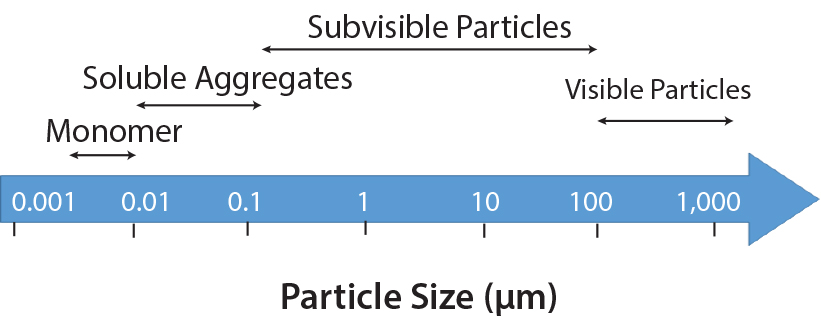
Featured Posts
-
Ukraine Russia Negotiations Trumps Call For Unconditional Talks
May 12, 2025 -
Uruguays Offshore Oil Exploration Challenges And Opportunities
May 12, 2025 -
Announcing The 2025 Astros Foundation College Classic All Tournament Team
May 12, 2025 -
Payton Pritchard How His Upbringing Shaped His Nba Success
May 12, 2025 -
Payton Pritchards Breakout Year A Deep Dive Into His Development
May 12, 2025