Overcoming Hurdles In Automated Visual Inspection Of Lyophilized Drug Products
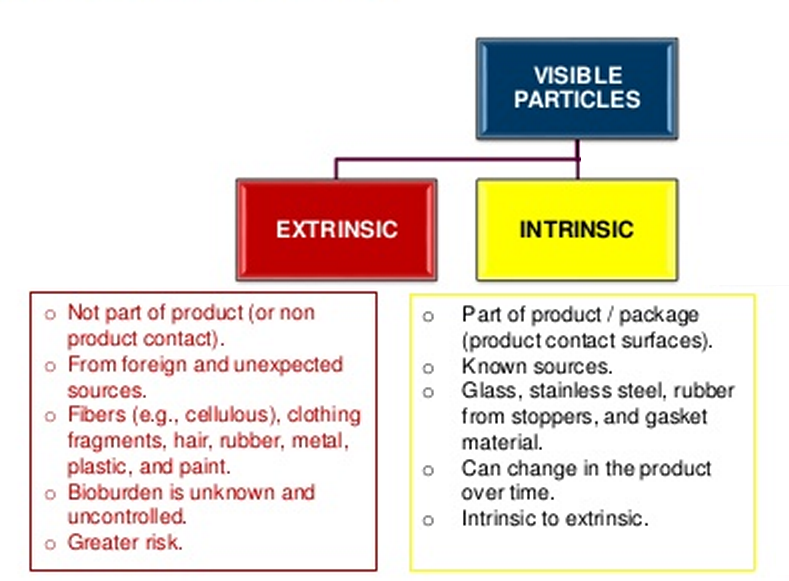
Table of Contents
Challenges in Imaging Lyophilized Products
Lyophilized drug products, also known as freeze-dried products, present unique challenges for automated visual inspection. The inherent variability in their appearance makes consistent and accurate automated detection a complex undertaking.
Variations in Appearance
Lyophilized cakes exhibit significant variability in appearance due to factors like formulation, freeze-drying process parameters, and storage conditions. This heterogeneity makes consistent automated detection incredibly difficult. Variations can lead to false positives and negatives, impacting the reliability of the inspection process.
- Variations in cake color and texture: Subtle color changes and textural differences can be challenging to detect consistently using traditional methods.
- Presence of cracks, fissures, or collapses: These defects, indicative of potential product instability, need to be reliably identified.
- Differences in sublimation patterns: Variations in the sublimation process leave distinct marks on the lyophilized cake, requiring sophisticated image analysis.
- The impact of different vial types and sizes: Variations in vial material, size, and shape can influence light reflection and shadowing, further complicating image analysis in automated visual inspection of lyophilized drug products.
Lighting and Image Acquisition
Achieving optimal lighting and capturing clear, high-resolution images of lyophilized cakes presents significant hurdles. Shadows, reflections, and uneven illumination can drastically impact inspection accuracy, leading to missed defects or false positives.
- Importance of consistent and controlled lighting: Uniform and controlled lighting is crucial to minimize shadows and reflections, ensuring consistent image quality.
- The use of specialized illumination techniques (e.g., diffuse lighting): Techniques like diffuse lighting can mitigate the impact of reflections from the vial and the lyophilized cake itself.
- Challenges in capturing images through glass vials: The curvature of the glass vial and potential refractive effects can distort the image, demanding advanced image correction techniques.
- Calibration and standardization of imaging systems: Regular calibration and standardization are vital for maintaining consistent image quality and inspection accuracy across different batches and systems.
Advanced Technologies for Enhanced Inspection
Overcoming the challenges of automated visual inspection of lyophilized drug products requires the implementation of advanced technologies. These innovations are crucial for improving accuracy, efficiency, and regulatory compliance.
AI and Machine Learning
The implementation of artificial intelligence (AI) and machine learning (ML) algorithms is transformative. These technologies enable the system to learn and adapt to the variability inherent in lyophilized cake appearance.
- Training AI models on large datasets of images: Extensive datasets of images representing various acceptable and defective lyophilized cakes are essential for training robust AI models.
- Using deep learning for defect classification: Deep learning algorithms are particularly well-suited to identify subtle variations and complex defects in lyophilized cakes.
- The use of computer vision techniques for image analysis: Computer vision techniques are used to automatically analyze images and identify deviations from predefined quality standards.
- Continuous improvement through model retraining: Regular retraining of AI models with new data ensures ongoing adaptation to evolving product characteristics and defect types.
Improved Image Processing Techniques
Sophisticated image processing techniques further enhance image quality and improve the accuracy of defect detection. These techniques address the inherent challenges presented by the variability of lyophilized products.
- Noise reduction techniques: Noise reduction algorithms minimize background noise and improve image clarity, leading to more accurate defect identification.
- Image enhancement algorithms: These algorithms enhance image contrast and sharpness, making it easier to detect subtle defects.
- Advanced segmentation methods for identifying defects: Advanced segmentation algorithms precisely delineate defects from the surrounding product, improving accuracy and reducing false positives.
- 3D imaging for improved defect characterization: 3D imaging allows for a more comprehensive characterization of defects, providing detailed information about their size, shape, and location.
Validation and Regulatory Compliance
Thorough validation and adherence to regulatory requirements are paramount for successful implementation of AVI systems for lyophilized drug products.
Validation of AVI Systems
Rigorous validation is crucial to demonstrate the accuracy and reliability of AVI systems, ensuring compliance with regulatory expectations.
- Qualification of the hardware and software components: This ensures the system performs as intended and meets specified requirements.
- Development and execution of validation protocols: Comprehensive validation protocols ensure the system accurately detects defects and minimizes false positives and negatives.
- Demonstrating accuracy and precision through testing: Testing with known good and defective samples demonstrates the system's accuracy and precision.
- Meeting regulatory expectations for data integrity: The system must adhere to strict data integrity guidelines to ensure reliable and auditable results.
Data Management and Traceability
Effective data management and traceability are essential for ensuring compliance and providing evidence of inspection results.
- Implementing robust data management systems: A robust system is necessary for storing, managing, and retrieving inspection data.
- Ensuring data integrity and security: Data integrity and security are crucial for ensuring the reliability and trustworthiness of inspection results.
- Maintaining audit trails and documentation: Complete documentation of all inspection processes and results is necessary for regulatory compliance.
- Compliance with 21 CFR Part 11 and other relevant regulations: Adherence to relevant regulatory guidelines ensures compliance and provides confidence in inspection results.
Conclusion
Automated visual inspection (AVI) is transforming the quality control of lyophilized drug products, despite the initial challenges. By leveraging advanced technologies like AI, superior image processing techniques, and stringent validation procedures, the pharmaceutical industry can overcome these hurdles and achieve greater efficiency and accuracy in inspection. Successful implementation requires a multifaceted approach that addresses the complexities of image acquisition, analysis, and regulatory compliance. Embrace the power of automated visual inspection of lyophilized drug products to ensure consistent quality and patient safety. Invest in advanced AVI systems today and optimize your lyophilization process for superior results. Don't hesitate to explore the latest advancements in automated visual inspection technology to improve your quality control processes and ensure the highest standards for your lyophilized drug products.
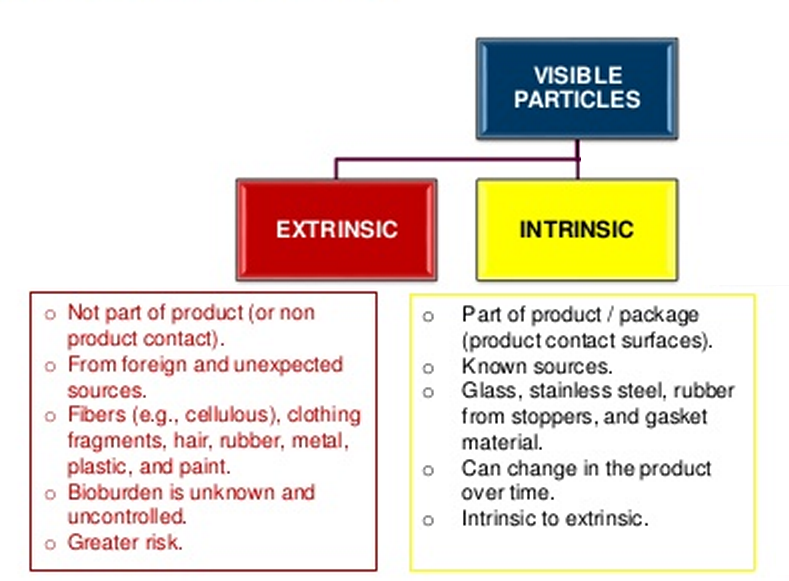
Featured Posts
-
Aaron Judge Ties Babe Ruths Yankees Record A Historic Achievement
May 12, 2025 -
Recent Decrease In Santorini Earthquakes What Scientists Say About The Future
May 12, 2025 -
Uruguay Apuesta Por China Un Regalo Inusual Para El Crecimiento De Sus Exportaciones Ganaderas
May 12, 2025 -
Mtv Cribs A Look Inside Mind Blowing Mansions
May 12, 2025 -
Canada Us Tariffs Ambassador Hints At Partial Removal
May 12, 2025