Reviving American Manufacturing: Who Will Fill The Factory Jobs?
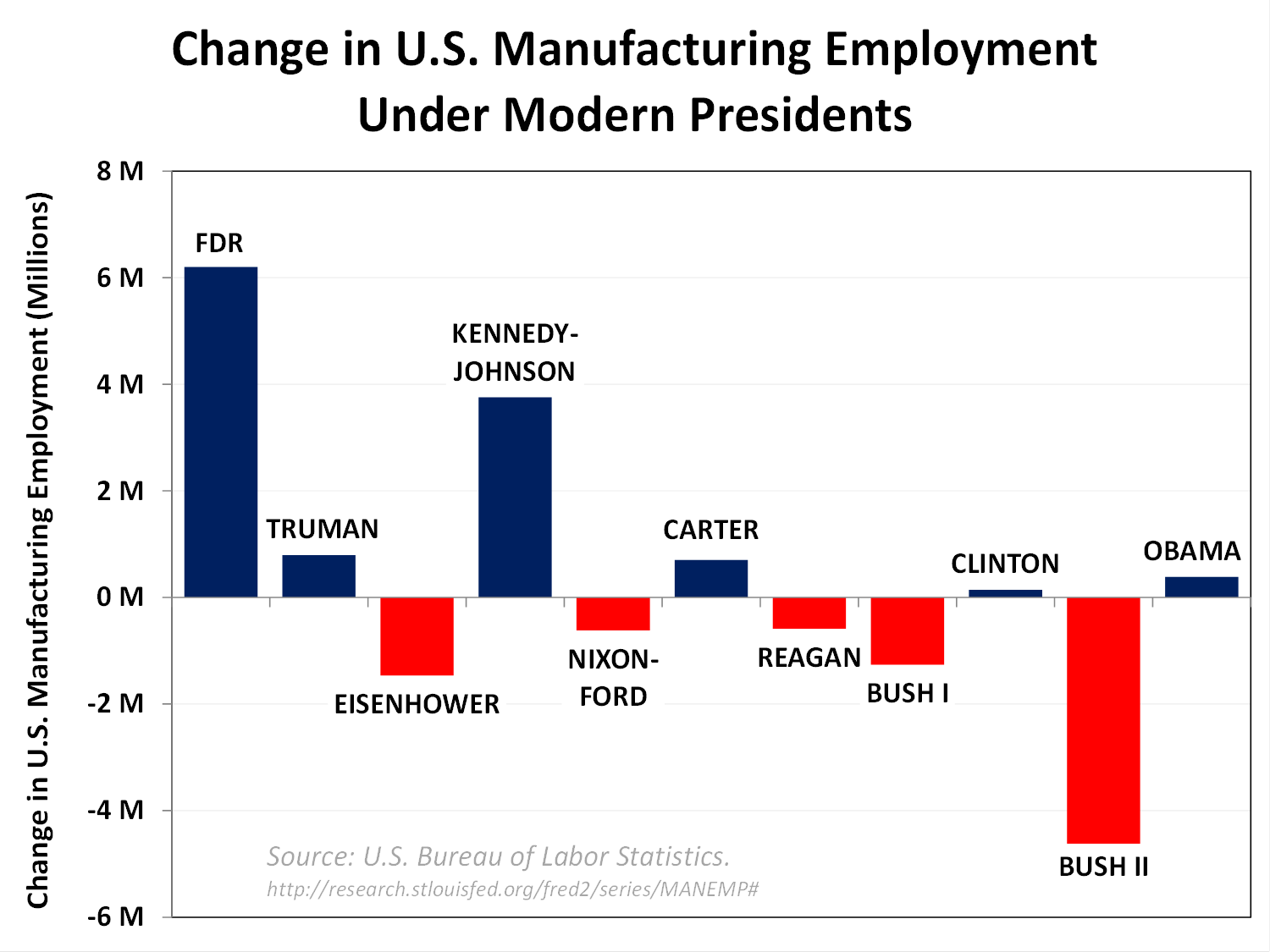
Table of Contents
The Skills Gap in American Manufacturing
A significant mismatch exists between the skills possessed by the available workforce and the demands of modern manufacturing. This skills gap is a major impediment to the revitalization of American manufacturing. Many available workers lack the necessary technical skills, while the educational system has often failed to keep pace with the rapidly evolving needs of the industry. This skills deficit manifests in several key areas:
- Outdated educational systems: Traditional vocational training programs haven't always kept pace with the technological advancements in modern manufacturing. Curriculum often lags behind the skills required for jobs in robotics, automation, and advanced materials processing.
- Lack of awareness: Many young people and career changers are unaware of the diverse and rewarding career paths available in modern manufacturing. The perception of manufacturing jobs as dirty, dangerous, and low-paying persists, deterring potential candidates.
- Limited access to reskilling and upskilling: Affordable and effective reskilling and upskilling programs are crucial for unemployed and underemployed workers. The lack of accessible and affordable training options further exacerbates the skills shortage.
- Demand for advanced technical skills: Modern manufacturing demands advanced technical skills, including proficiency in robotics, automation, data analysis, and sophisticated computer-aided design (CAD) software. These advanced manufacturing skills require specialized training and ongoing professional development.
Attracting and Retaining a New Generation of Manufacturing Workers
Attracting younger generations to manufacturing careers requires a fundamental shift in perception and a proactive approach to recruitment and retention. The industry needs to present itself as a modern, dynamic, and rewarding career path, highlighting the innovative technologies and the opportunities for growth. Here are some key strategies:
- Promoting positive narratives: Manufacturing companies must actively promote a positive image of the industry. Showcasing modern, clean, and technologically advanced facilities is vital to dispel outdated stereotypes. Highlighting the problem-solving and creative aspects of the work can be highly effective.
- Competitive salaries and benefits: Offering competitive salaries, comprehensive healthcare plans, and robust retirement packages is crucial to attract and retain talent. Benefits should reflect the value placed on employees.
- Improved work-life balance: Creating a positive and inclusive work environment with opportunities for work-life balance is crucial for attracting and retaining employees. Flexible schedules and family-friendly policies can make a significant difference.
- Career growth and development: Highlighting opportunities for career advancement and professional development is vital. Investing in employee training and providing opportunities for skill enhancement demonstrates a commitment to long-term employee success.
The Role of Automation and Technological Advancements
Automation and Industry 4.0 technologies are transforming the manufacturing landscape. While automation may displace some jobs, it also creates new opportunities requiring a different skill set. The workforce must adapt and acquire new skills to meet the demands of this technological shift.
- Skilled technicians: The demand for skilled technicians to maintain, operate, and troubleshoot advanced manufacturing equipment, including robots and automated systems, is increasing rapidly. This necessitates specialized training in areas like mechatronics and robotics maintenance.
- Data analytics and process optimization: Workers with expertise in data analytics and process optimization are increasingly valuable. The ability to analyze data to improve efficiency, reduce waste, and enhance product quality is crucial.
- Digital literacy and Industry 4.0 technologies: Investing in training programs focused on digital literacy and Industry 4.0 technologies, including the Industrial Internet of Things (IIoT), cloud computing, and cybersecurity, is essential.
- Addressing job displacement concerns: Proactive reskilling initiatives are crucial to address concerns about job displacement due to automation. Retraining programs can equip workers with the skills needed for new roles within the evolving manufacturing environment.
Government Initiatives and Private Sector Partnerships
Government funding and private sector partnerships play a pivotal role in bridging the skills gap. Collaborative efforts are essential to create effective and accessible workforce development programs.
- Government funding for training programs: Government funding for apprenticeship programs, vocational training centers, and reskilling initiatives is critical for providing resources and expanding training opportunities.
- Public-private partnerships: Public-private partnerships facilitate the development and implementation of effective training programs that align with industry needs. Collaboration ensures that training is relevant and practical.
- Tax incentives for employee training: Tax incentives for companies that invest in employee training and development can encourage private sector investment in workforce development.
- Collaboration between educational institutions and companies: Close collaboration between educational institutions and manufacturing companies is vital for creating relevant curriculum and ensuring that graduates possess the necessary skills for employment.
Conclusion
Reviving American manufacturing is not just about building new factories; it's about building a skilled workforce capable of operating them efficiently and innovatively. Addressing the skills gap, attracting a new generation of skilled workers, and adapting to technological advancements requires a concerted effort from government, industry, and educational institutions. Successfully filling factory jobs hinges on effective workforce development initiatives, strategic public-private partnerships, and a commitment to creating a positive and rewarding work environment in the manufacturing sector. Invest in the future of American manufacturing by supporting workforce development programs and creating a skilled workforce ready to fill the growing number of factory jobs. Let's build a robust and thriving American manufacturing sector together!
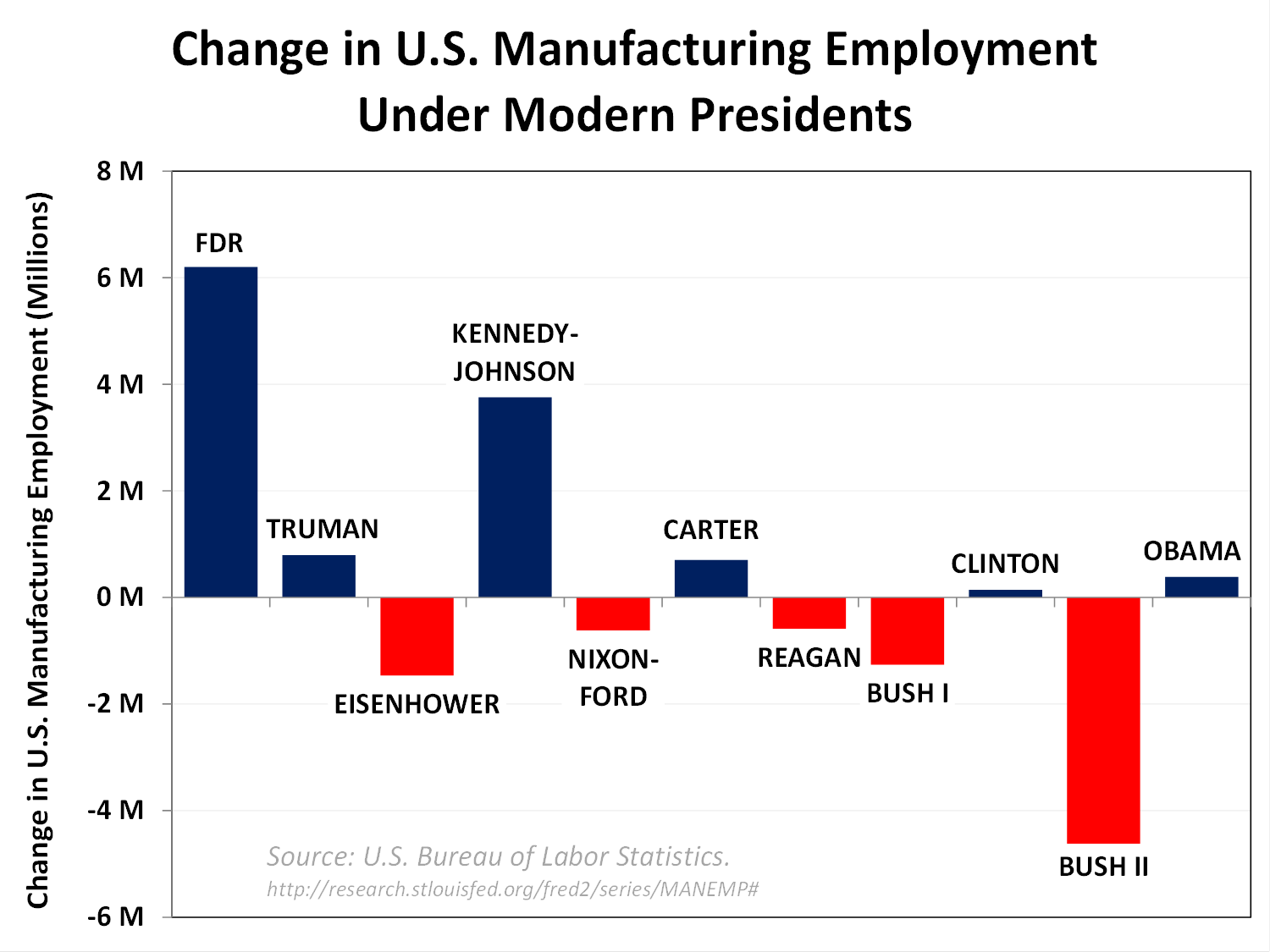
Featured Posts
-
The Goldbergs Exploring The Shows Best Episodes And Running Gags
May 21, 2025 -
Bbc Antiques Roadshow Couples Illegal National Treasure Trade Results In Prison Sentence
May 21, 2025 -
Home Buying In A Changing Climate Navigating Credit Risk
May 21, 2025 -
Provence Hiking Itinerary Mountain To Coast Self Guided Trek
May 21, 2025 -
Stephane La Conquete Parisienne D Une Chanteuse Suisse
May 21, 2025
Latest Posts
-
I Megali Tessarakosti Esperida Stin Patriarxiki Ekklisiastiki Akadimia Kritis
May 21, 2025 -
Mls I Pithanotita Epistrofis Toy Giakoymaki
May 21, 2025 -
Efimeries Iatron Stin Patra Savvatokyriako
May 21, 2025 -
Symvoylio Megalis Tessarakostis Ekdilosi Stin Patriarxiki Akadimia Kritis
May 21, 2025 -
Patra Efimereyontes Iatroi Savvatokyriako
May 21, 2025