Strategies For Successful Automated Visual Inspection Of Lyophilized Pharmaceuticals
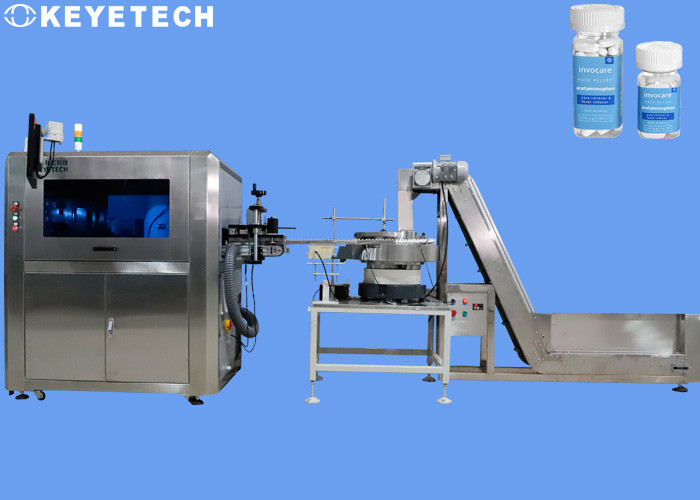
Table of Contents
Selecting the Right Automated Visual Inspection System for Lyophilized Pharmaceuticals
Choosing the right automated visual inspection system is paramount for effective quality control. The unique characteristics of lyophilized products demand careful consideration.
Understanding Lyophilized Product Characteristics
Lyophilized pharmaceuticals, due to their freeze-drying process, present unique visual challenges. Identifying and addressing these challenges is crucial for selecting the appropriate inspection system.
- Specific examples of defects in lyophilized pharmaceuticals: Cracks, collapses, discolorations, particulate matter, missing labels, and vial damage.
- Considerations for different lyophilized dosage forms: The inspection system must be adaptable to various formats, including vials of different sizes, shapes, and materials, as well as pre-filled syringes. The system's ability to handle these variations is key.
Key Features of Automated Visual Inspection Systems
A robust automated visual inspection system for lyophilized products should include several essential features:
- Examples of different imaging technologies: High-resolution machine vision systems are commonly used, offering detailed images. Spectral imaging can provide additional information about the product's composition and detect subtle defects.
- Importance of AI and machine learning in defect classification: Advanced algorithms, often incorporating AI and machine learning, are essential for accurately identifying and classifying a wide range of defects, including those that are subtle or difficult for the human eye to detect. This increases both speed and accuracy. Deep learning models, for example, can be trained on large datasets of images to achieve high levels of accuracy.
Validation and Regulatory Compliance
Validation and regulatory compliance are non-negotiable aspects of implementing an automated visual inspection system.
- Steps involved in system validation and qualification: This includes installation qualification (IQ), operational qualification (OQ), and performance qualification (PQ) to demonstrate the system consistently meets pre-defined specifications.
- Documentation requirements for regulatory compliance: Meticulous documentation is crucial for meeting FDA 21 CFR Part 11 and other relevant regulatory guidelines. This includes maintaining detailed records of system performance, calibration, and maintenance.
Optimizing the Automated Visual Inspection Process
Optimizing the entire process from sample preparation to data analysis is critical for maximizing the effectiveness of your automated visual inspection system.
Pre-Inspection Preparation
Careful sample handling is crucial for accurate results.
- Procedures for cleaning and handling vials before inspection: Establishing standardized procedures for cleaning and handling vials minimizes the risk of contamination and ensures consistent inspection results. This might include using specialized cleaning solutions and robotics to automate handling.
- Minimizing potential contamination during sample preparation: Implementing cleanroom protocols and using appropriate personal protective equipment (PPE) are essential for maintaining product integrity.
Image Acquisition and Processing
Image quality directly impacts the accuracy of defect detection.
- Techniques for optimizing lighting and camera settings: Appropriate lighting and camera settings are critical for capturing clear, high-resolution images. This might involve using specialized lighting techniques like coaxial illumination to minimize shadows and reflections.
- Algorithms for noise reduction, image enhancement, and defect segmentation: Advanced image processing algorithms are employed to enhance image clarity, reduce noise, and accurately segment regions of interest for defect detection.
Data Analysis and Reporting
Effective data analysis provides valuable insights for continuous improvement.
- Data visualization techniques for summarizing inspection results: Data visualization tools, such as charts and graphs, help summarize inspection results clearly and effectively, allowing for easy identification of trends and patterns.
- Generating reports compliant with regulatory requirements: The system should generate comprehensive reports that meet all regulatory requirements, including traceability and audit trails. These reports should be easily exportable and readily available for audits.
Cost-Effectiveness and ROI of Automated Visual Inspection
Implementing an automated system provides significant long-term cost savings.
- Cost savings from reduced labor costs and improved efficiency: Automation significantly reduces labor costs associated with manual inspection while increasing throughput and efficiency.
- Reduced product waste and improved quality control: Early detection of defects minimizes product waste and enhances overall product quality, leading to increased customer satisfaction.
- Improved regulatory compliance and risk mitigation: Automated systems improve regulatory compliance by providing robust documentation and minimizing the risk of human error.
Conclusion
Successful Automated Visual Inspection of Lyophilized Pharmaceuticals relies on a strategic approach encompassing the selection of a suitable system, process optimization, and rigorous data analysis. By carefully considering the unique characteristics of lyophilized products, implementing best practices, and leveraging advanced technologies such as AI and machine learning, pharmaceutical manufacturers can significantly enhance the efficiency, accuracy, and regulatory compliance of their visual inspection processes. To learn more about implementing Automated Visual Inspection systems for Lyophilized products and maximizing the benefits of Automated Visual Inspection in Lyophilization, contact a specialized provider for consultation today.
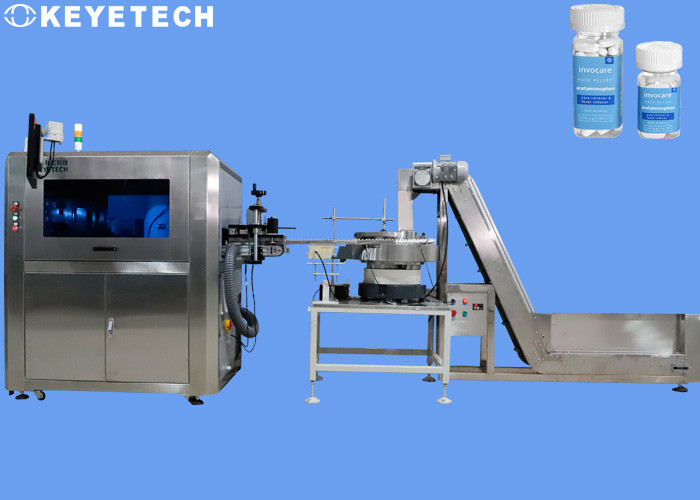
Featured Posts
-
Experience The John Wick World A Baba Yaga Transformation In Las Vegas
May 12, 2025 -
Une Rencontre Artistique Sylvester Stallone Et Mon Exposition
May 12, 2025 -
Mtv Movie And Tv Awards A 2025 Absence
May 12, 2025 -
Yankees Vs Rays Key Injuries Impacting The Series May 2 4
May 12, 2025 -
Former Ufc Champion Jose Aldo Targets Featherweight Division
May 12, 2025