The Future Of Automated Visual Inspection In Lyophilized Vial Manufacturing
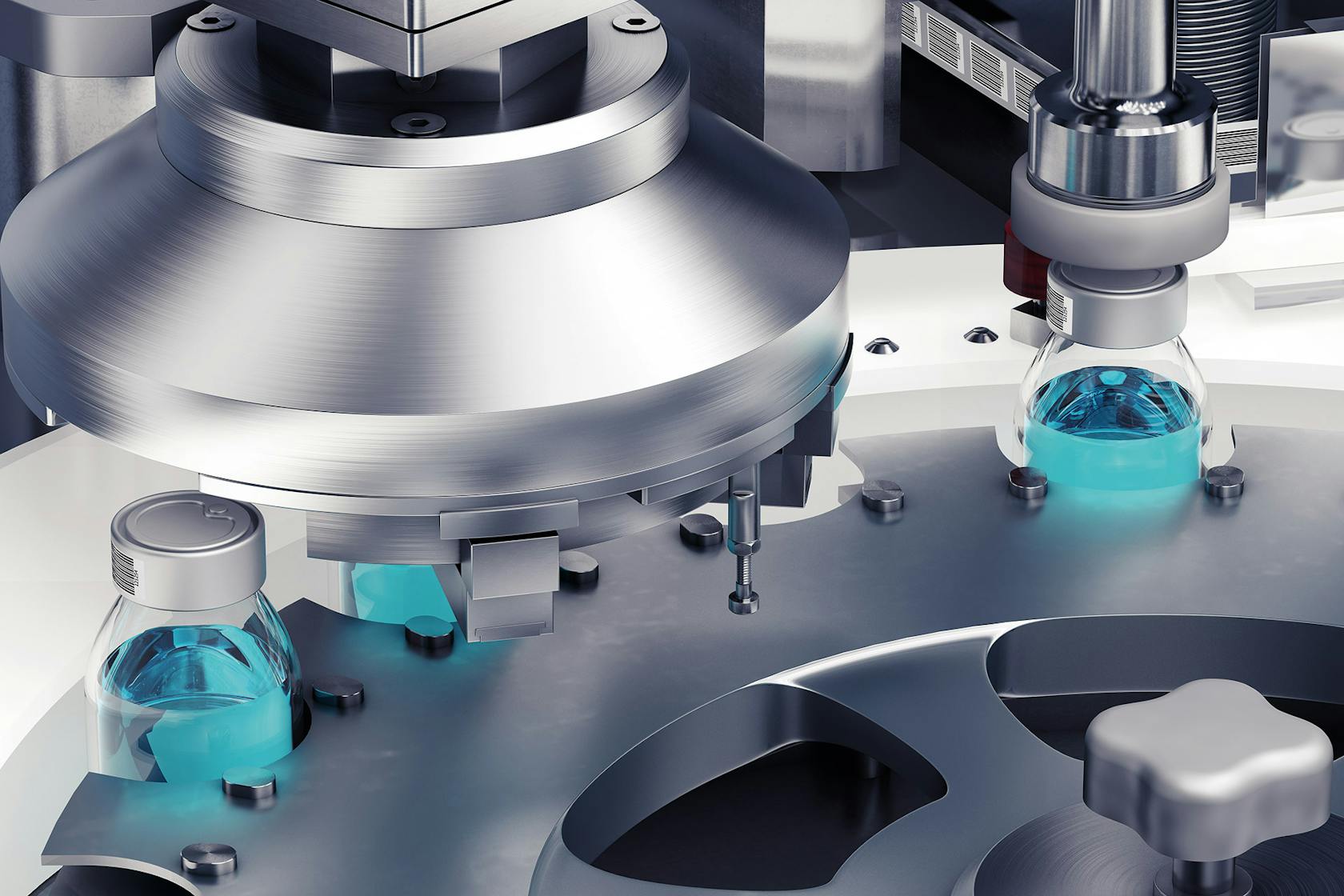
Table of Contents
Enhanced Accuracy and Reduced Human Error in Lyophilized Vial Inspection
Manual inspection of lyophilized vials is inherently limited. Human inspectors are susceptible to fatigue, leading to inconsistencies and missed defects. Subtle flaws like minute particulate matter, hairline cracks, or slight fill level discrepancies can easily be overlooked, resulting in compromised product quality and potential safety risks. This is where automated visual inspection systems excel.
Automated systems offer several key advantages:
- Increased speed and throughput: Automated systems can inspect hundreds or even thousands of vials per hour, significantly increasing production efficiency compared to manual methods.
- Objective and consistent defect detection: Unlike human inspectors, automated systems maintain consistent performance throughout the inspection process, ensuring objective and unbiased defect detection.
- Reduced labor costs: Automation reduces the need for a large workforce dedicated to manual inspection, leading to considerable cost savings in the long run.
- Improved overall product quality: By identifying and rejecting defective vials early in the process, automated systems contribute to a significant improvement in overall product quality and reduce the risk of recalls.
Various automated inspection technologies are employed, including:
- Machine vision systems: These systems use high-resolution cameras and sophisticated image processing algorithms to capture detailed images of each vial. The algorithms then analyze these images to detect defects such as particulate matter, cracks in the vial glass, fill level inconsistencies, and label misalignment.
- AI-powered systems: Artificial intelligence, particularly deep learning algorithms, further enhance the accuracy and adaptability of inspection systems. These systems learn from vast datasets of previously inspected vials, enabling them to identify even subtle defects that might be missed by traditional machine vision systems. This self-learning capability leads to a significant reduction in false positives and improves overall efficiency.
Advanced Technologies Driving Automation in Lyophilized Vial Inspection
Several advanced technologies are driving the automation revolution in lyophilized vial inspection:
Machine Vision Systems
Machine vision systems are the cornerstone of automated visual inspection. They utilize high-resolution cameras and advanced image processing algorithms to analyze vial images with exceptional precision. These systems can effectively detect a wide range of defects including:
- Particulate matter: Detection of foreign particles within the lyophilized product.
- Vial cracks: Identification of cracks or fissures in the vial glass, indicating potential leakage or compromised sterility.
- Label misalignment: Ensuring accurate and consistent label placement on the vials.
- Fill level variations: Precise measurement of the lyophilized product fill level to ensure consistency across all vials.
Artificial Intelligence (AI) and Deep Learning
AI and deep learning are transforming automated visual inspection by significantly improving the accuracy and adaptability of inspection systems. Deep learning algorithms can learn from massive datasets of images, identifying complex patterns and subtle defects that may be undetectable by traditional algorithms. This leads to:
- Improved defect detection accuracy: AI significantly reduces false positives and false negatives, ensuring a higher level of accuracy in defect detection.
- Enhanced adaptability: AI-powered systems can adapt to variations in lighting conditions, vial types, and product characteristics, ensuring consistent performance across different production runs.
- Predictive maintenance: AI can also be used to predict potential equipment malfunctions, minimizing downtime and improving overall system reliability.
Integration with Existing Manufacturing Lines
Modern automated visual inspection systems are designed for seamless integration into existing lyophilization lines. This ensures minimal disruption to the existing workflow and maximizes the efficiency of the entire manufacturing process. The integration typically involves:
- Automated feeding and handling systems: Efficiently transferring vials from the lyophilizer to the inspection system and vice versa.
- Data integration with existing systems: Seamlessly integrating inspection data with the overall manufacturing execution system (MES) for comprehensive data management and traceability.
- Modular design: Allowing for flexible integration into various production line configurations.
Regulatory Compliance and Data Management in Automated Visual Inspection
Adherence to regulatory standards is paramount in pharmaceutical manufacturing. Automated visual inspection systems must comply with regulations such as FDA 21 CFR Part 11 and Good Manufacturing Practices (GMP) guidelines. Key data management features ensuring compliance include:
- Automated data logging and traceability: Complete and auditable records of every vial inspected, including images of detected defects and inspection results.
- Secure data storage and retrieval: Secure storage of inspection data to prevent unauthorized access and ensure data integrity.
- Audit trail generation: A complete audit trail of all system activities, including user actions, system modifications, and data changes.
- Reporting and analysis capabilities: Generating comprehensive reports for process optimization and regulatory compliance purposes.
The Cost-Effectiveness of Automated Visual Inspection in Lyophilized Vial Manufacturing
While the initial investment in automated visual inspection systems can be significant, the long-term cost savings are substantial. The ROI is driven by:
- Reduction in labor costs: Automated systems significantly reduce the need for manual inspection, leading to substantial savings in labor costs.
- Waste reduction: Improved quality control minimizes waste due to defective products, further reducing costs.
- Increased production capacity: Higher throughput achieved through automation allows for increased production capacity without expanding the workforce.
The return on investment (ROI) from implementing automated visual inspection is typically realized within a relatively short timeframe, making it a financially sound decision for pharmaceutical manufacturers seeking to improve efficiency and quality.
Conclusion
The future of lyophilized vial manufacturing relies heavily on the implementation of automated visual inspection systems. These systems offer significantly improved accuracy, efficiency, and compliance compared to traditional manual methods. By leveraging advanced technologies like machine vision and AI, pharmaceutical manufacturers can enhance product quality, reduce costs, and maintain regulatory compliance. Embrace the future of lyophilized vial production by investigating and implementing automated visual inspection solutions for your operations. Contact us today to learn more about how automated visual inspection can benefit your lyophilized vial manufacturing process.
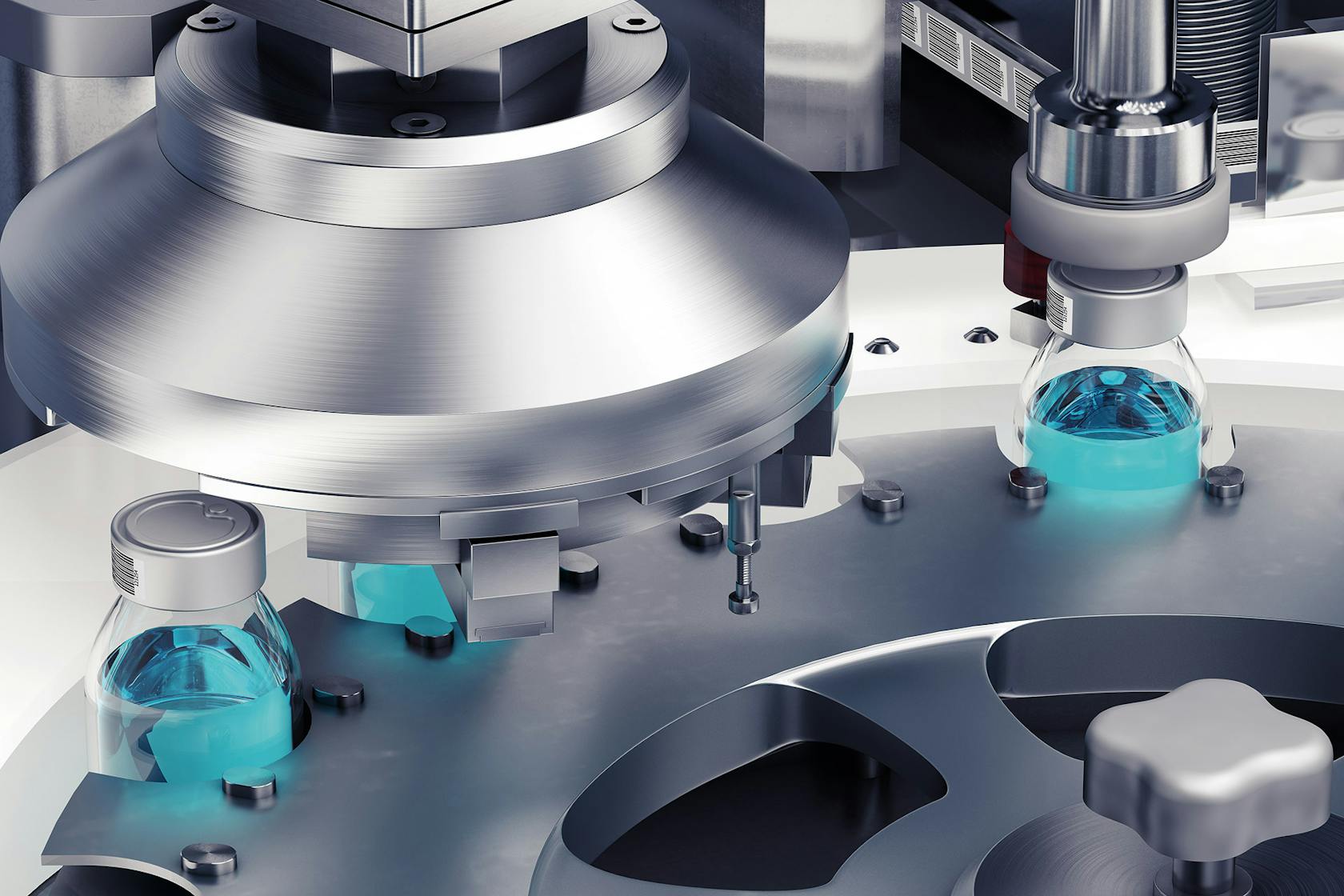
Featured Posts
-
Night Hunter Essential Gear And Equipment For Nighttime Hunts
May 12, 2025 -
Is Conor Mc Gregors Relationship With Fox News Beneficial
May 12, 2025 -
Benny Blanco And Selena Gomez Addressing The Cheating Rumors Involving Theresa Marie
May 12, 2025 -
Chicago Bulls Vs New York Knicks Latest Injury Reports
May 12, 2025 -
Dechiffrage Economique La Resistance De L Euro Malgre Les Crises
May 12, 2025