The Great Decoupling And The Future Of Manufacturing
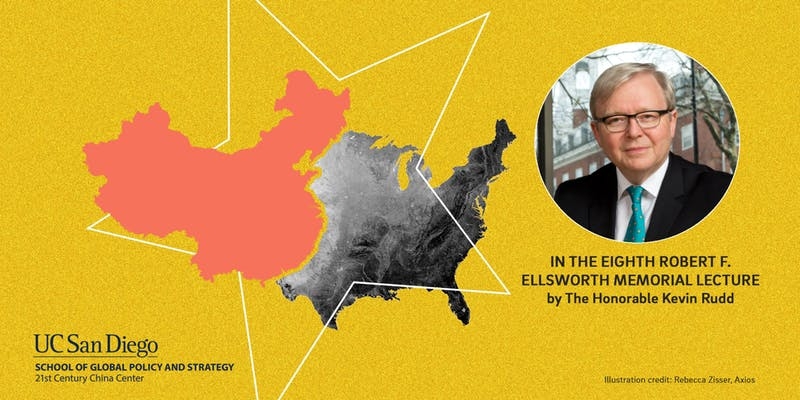
Table of Contents
The Drivers of the Great Decoupling
Several interconnected factors have fueled the Great Decoupling, fundamentally altering the global manufacturing landscape.
Geopolitical Instability and Trade Wars
Increased geopolitical tensions and escalating trade wars have significantly disrupted globally integrated supply chains.
- Increased Tariffs and Trade Restrictions: The imposition of tariffs and trade restrictions, exemplified by the US-China trade war, has forced companies to reconsider their reliance on single-source suppliers in specific regions. This has led to increased costs and logistical complexities.
- Political Tensions: Geopolitical instability and political risks in various regions have created uncertainty and disruptions, highlighting the vulnerability of long, complex supply chains. This includes political instability, sanctions, and regional conflicts.
- Supply Chain Resilience: Businesses are now prioritizing supply chain resilience, seeking to mitigate geopolitical risk and reduce their dependence on potentially unstable regions.
Keywords: supply chain resilience, geopolitical risk, trade protectionism, trade wars, tariffs, sanctions
Pandemic-Induced Supply Chain Disruptions
The COVID-19 pandemic starkly revealed the fragility of globally extended supply chains.
- Port Congestion and Factory Closures: Lockdowns and restrictions caused widespread port congestion, factory closures, and transportation bottlenecks, leading to significant delays and shortages.
- Supply Chain Vulnerability: The pandemic underscored the vulnerability of relying heavily on single-source suppliers located in geographically concentrated areas.
- Risk Mitigation: Companies are now implementing strategies for risk mitigation and pandemic resilience, including diversifying their supply bases and investing in more robust logistics systems.
Keywords: supply chain vulnerability, pandemic resilience, risk mitigation, supply chain disruptions, logistics, bottlenecks
Sustainability Concerns and Environmental Regulations
Growing environmental awareness and stricter regulations are pushing companies to shorten their supply chains.
- Reduced Carbon Footprint: The pressure to reduce carbon emissions associated with transportation is driving a shift towards regionalized production, minimizing the environmental impact of long-distance shipping.
- Ethical Sourcing: Consumers are increasingly demanding ethically sourced products, putting pressure on companies to improve transparency and traceability throughout their supply chains, often facilitated by proximity.
- Green Supply Chains: The adoption of circular economy principles and the development of green supply chains are pushing for more localized production and waste reduction.
Keywords: sustainable manufacturing, circular economy, green supply chains, carbon footprint, ethical sourcing, supply chain transparency
The Impact on Manufacturing Strategies
The Great Decoupling is fundamentally reshaping manufacturing strategies, leading to significant changes in how companies design, source, and manage their operations.
Nearshoring and Reshoring Initiatives
Companies are actively exploring nearshoring and reshoring strategies to mitigate risks and improve supply chain agility.
- Nearshoring Strategies: Many companies are moving production to nearby countries, reducing transportation costs and lead times while still benefiting from lower labor costs compared to domestic production.
- Reshoring Benefits: Some companies are bringing manufacturing back to their home countries, prioritizing factors like greater control over production, improved quality control, and enhanced responsiveness to market demands, even if at a higher cost.
- Regional Supply Chains: The focus is shifting to building more regionalized supply chains, fostering collaboration and reducing dependence on distant suppliers. Examples include automotive manufacturers establishing regional production hubs and electronics companies moving assembly closer to key markets.
Keywords: nearshoring strategies, reshoring benefits, regional supply chains, regionalization, supply chain agility
Automation and Digitalization
Investment in automation and digitalization is accelerating to enhance efficiency and improve supply chain visibility.
- Industry 4.0: Companies are embracing Industry 4.0 technologies like robotics, AI, and IoT to automate processes, optimize production, and improve overall efficiency.
- Automation in Manufacturing: Automation is reducing reliance on human labor for repetitive tasks, increasing productivity and improving consistency.
- Smart Factories: The adoption of smart factories with interconnected systems is enhancing supply chain visibility and enabling real-time monitoring and control.
Keywords: Industry 4.0, automation in manufacturing, smart factories, robotics, AI, IoT, supply chain visibility
Supply Chain Diversification and Resilience
Companies are implementing strategies to diversify their supplier base and build more resilient supply chains.
- Supply Chain Diversification: Reducing reliance on single suppliers and establishing multiple sourcing options minimizes the impact of disruptions affecting individual suppliers.
- Risk Management: Sophisticated risk assessment tools and processes are being implemented to identify and mitigate potential disruptions proactively.
- Supply Chain Visibility: Real-time tracking and data analytics provide enhanced visibility across the supply chain, enabling faster responses to unexpected events.
Keywords: supply chain diversification, risk management, supply chain visibility, supply chain mapping, supplier relationship management
Challenges and Opportunities in the New Manufacturing Landscape
The transition to a more regionalized and resilient manufacturing sector presents both challenges and opportunities.
Increased Costs and Labor Shortages
Nearshoring and reshoring can lead to higher production costs and potential labor shortages.
- Higher Labor Costs: Relocating manufacturing to higher-cost regions requires careful cost analysis and potential trade-offs.
- Skilled Labor Shortages: Finding skilled labor in certain regions can be challenging, requiring investment in training and upskilling initiatives.
Technological Innovation and Skill Development
Investing in technological innovation and upskilling the workforce is crucial for success in the new manufacturing landscape.
- Technological Advancements: Continuous investment in cutting-edge technologies is essential to maintain a competitive edge and improve operational efficiency.
- Reskilling and Upskilling: Training programs and initiatives to upskill and reskill the workforce are crucial to adapt to the changing demands of the new manufacturing environment.
Government Policies and Incentives
Government policies and incentives play a vital role in supporting the transition to a more resilient manufacturing sector.
- Reshoring Incentives: Governments are offering various incentives to encourage companies to reshore manufacturing activities.
- Infrastructure Investments: Investments in infrastructure, such as improved transportation networks and advanced technology hubs, are essential to support the growth of a regionalized manufacturing sector.
Conclusion: Navigating the Future of Manufacturing in the Age of Decoupling
The Great Decoupling is fundamentally reshaping the global manufacturing landscape. Driven by geopolitical instability, pandemic disruptions, and sustainability concerns, companies are actively adopting new strategies, including nearshoring, reshoring, automation, and supply chain diversification. While this transition presents challenges like increased costs and labor shortages, it also unlocks significant opportunities for innovation, resilience, and sustainable growth. Understanding the Great Decoupling and its impact on global manufacturing is crucial for businesses to adapt and thrive. Start exploring strategies for building more resilient and sustainable supply chains today. Learn more about building resilient supply chains and navigating the changing landscape of global manufacturing by exploring resources dedicated to [link to relevant resources].
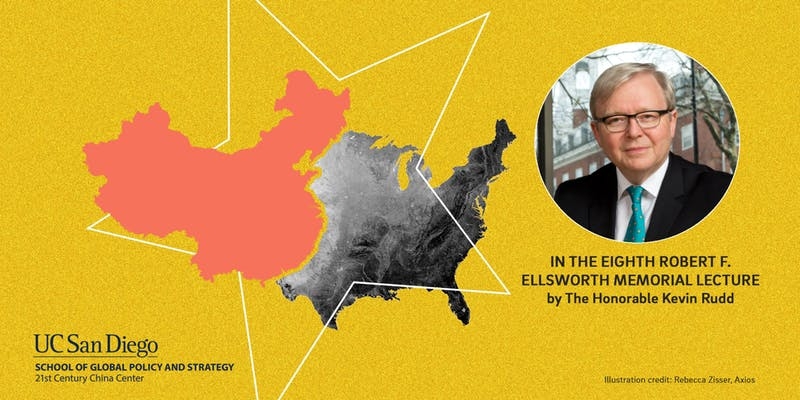
Featured Posts
-
Psg Nantes Maci 1 1 Berabere Sonuc
May 08, 2025 -
Watch Andor Season 1 Hulu And You Tube Streaming Options Available
May 08, 2025 -
76
May 08, 2025 -
Googles Search Chief Sounds Alarm Doj Proposals And The Erosion Of User Trust
May 08, 2025 -
Renewed Trade War Concerns Upcoming Meeting Between U S And Chinese Officials
May 08, 2025