U.S. Companies Slash Costs Amid Tariff Uncertainty
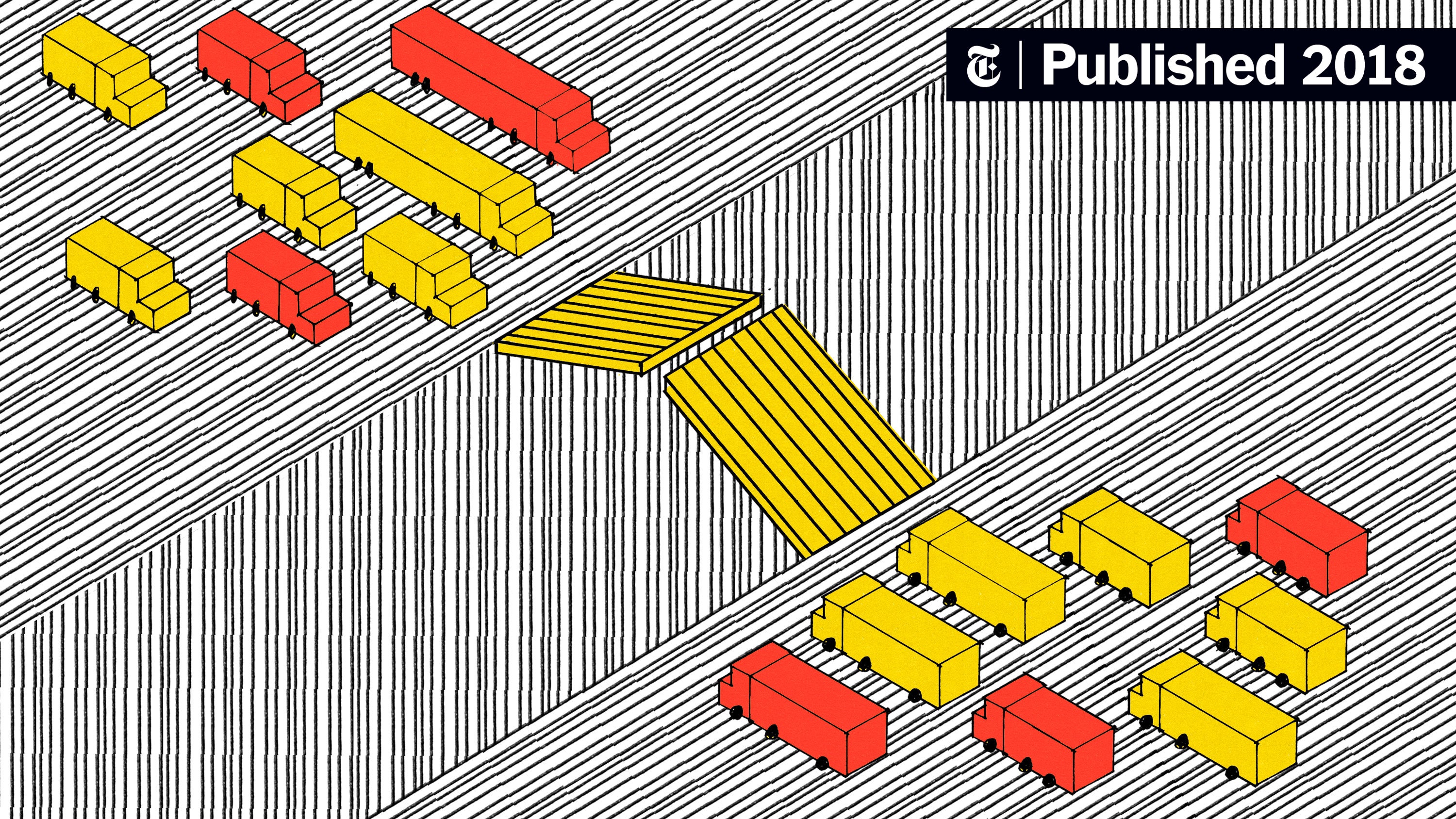
Table of Contents
Strategies for Reducing Operational Costs
Faced with increased import costs and unpredictable tariff policies, U.S. businesses are employing a range of strategies to reduce operational expenses. These efforts are crucial for maintaining profitability and competitiveness in the global marketplace.
Supply Chain Diversification
A key response to tariff uncertainty is the diversification of supply chains. Companies are actively moving away from relying on single-source suppliers, especially those located in countries imposing high tariffs.
- Nearshoring: Relocating manufacturing or sourcing to nearby countries.
- Reshoring: Bringing manufacturing back to the U.S.
- Exploring alternative suppliers: Identifying and partnering with suppliers in regions with more favorable tariff policies or lower production costs.
Diversifying supply chains offers several benefits, including reduced reliance on volatile markets, potentially lower transportation costs, and access to alternative materials. However, challenges include higher initial investment costs and the need to establish robust quality control processes with new suppliers. Careful due diligence and strategic planning are essential for successful supply chain diversification.
Automation and Technological Upgrades
Automation is playing a critical role in helping U.S. companies reduce labor costs and increase efficiency. By implementing advanced technologies, businesses can streamline operations and minimize reliance on human labor in certain areas.
- Robotics: Automating repetitive tasks on assembly lines and in warehouses.
- AI-powered systems: Optimizing production processes, inventory management, and customer service.
- Advanced manufacturing techniques: Implementing lean manufacturing principles and other efficiency-enhancing methodologies.
While the initial investment in automation can be substantial, the long-term cost savings, increased productivity, and improved product quality often yield a significant return on investment (ROI). However, potential drawbacks include job displacement and the need for skilled workers to operate and maintain these sophisticated systems.
Negotiation with Suppliers
Building and maintaining strong relationships with suppliers is crucial for effectively negotiating better prices and payment terms. Strategic negotiation can significantly reduce operational costs.
- Consolidating orders: Negotiating lower per-unit costs by placing larger, consolidated orders.
- Leveraging market conditions: Negotiating favorable prices based on current market dynamics and competitor pricing.
- Seeking long-term contracts: Securing predictable pricing and supply through long-term agreements.
Effective negotiation requires understanding market trends, building trust with suppliers, and having a clear understanding of your own company's needs and leverage. Strong supplier relationships are essential for navigating economic uncertainty and ensuring a consistent flow of quality goods and services.
Impact on Different Sectors
The impact of tariff uncertainty and resulting cost-cutting measures varies across different sectors of the U.S. economy.
Manufacturing Industry
The manufacturing industry has been particularly hard-hit by tariffs, leading to widespread implementation of cost-cutting strategies.
- Lean manufacturing principles: Eliminating waste and optimizing production processes.
- Waste reduction initiatives: Implementing programs to minimize material waste, energy consumption, and production inefficiencies.
- Automation: Increased reliance on robotics and other automated systems to reduce labor costs.
The impact on manufacturing jobs has been significant, with some companies experiencing job losses due to automation and others relocating production facilities to lower-cost regions. Statistics from the Bureau of Labor Statistics paint a complex picture, showing job losses in some sectors offset by gains in others as companies adapt.
Retail and Consumer Goods
Retail companies are adjusting their pricing and inventory strategies to counter increased import costs resulting from tariffs.
- Price adjustments: Increasing prices to offset higher input costs, potentially impacting consumer demand.
- Reduced product offerings: Streamlining product lines to focus on higher-margin items.
- Promotional strategies: Implementing sales and discounts to maintain sales volume despite price increases.
Consumer spending habits are closely tied to tariff-induced price increases. Data from the U.S. Census Bureau and other sources indicate shifts in consumer behavior, with some consumers opting for less expensive alternatives or reducing overall spending.
Technology Sector
The tech industry is facing its own set of challenges, particularly regarding sourcing components and adjusting pricing models.
- Shifting production locations: Relocating manufacturing to regions with lower labor costs and more favorable trade policies.
- Price optimization: Implementing dynamic pricing strategies to balance profitability with consumer demand.
- Software solutions for efficiency: Utilizing software to improve process efficiency and reduce operational costs.
The impact of cost-cutting pressures on innovation is complex. While it can lead to streamlining and efficiency gains, it might also stifle innovation if companies prioritize cost reduction over investment in new technologies and research.
Long-Term Implications of Cost-Cutting Measures
The cost-cutting strategies employed by U.S. companies have significant long-term implications for both businesses and the economy.
Job Displacement and Economic Growth
Automation and other cost-cutting measures can lead to job displacement in certain sectors, impacting overall economic growth.
- Potential for job losses: Automation may lead to a reduction in certain types of jobs, particularly in manufacturing and other labor-intensive industries.
- Potential for job creation: New jobs may be created in other sectors, such as software development, data analysis, and automation technology.
- Impact on innovation: Cost-cutting pressures may stimulate innovation in some areas, while stifling it in others.
The net effect on employment and economic growth remains uncertain and depends on the rate of job creation in new sectors and the effectiveness of government policies aimed at supporting workers displaced by automation.
Impact on Competitiveness
Cost-cutting strategies can influence the competitiveness of U.S. companies in the global market.
- Improved efficiency: Cost-cutting can lead to increased efficiency and lower production costs, enhancing competitiveness.
- Reduced innovation: Focusing solely on cost reduction may lead to a reduction in investment in research and development, potentially hindering innovation and long-term competitiveness.
- Pricing strategies: Balancing price competitiveness with profitability is crucial for maintaining market share.
Maintaining competitiveness requires a balanced approach that combines cost-cutting measures with investments in innovation, technology, and skilled labor.
Conclusion: Navigating the Challenges of U.S. Companies Slashing Costs Amid Tariff Uncertainty
U.S. companies are actively employing various cost-cutting strategies—supply chain diversification, automation, and supplier negotiations—in response to tariff uncertainty. These measures have varying impacts across different sectors, including manufacturing, retail, and technology. The long-term implications include potential job displacement, but also opportunities for increased efficiency and innovation. The adaptability and resilience of U.S. businesses are being tested, yet their ability to innovate and adjust will ultimately determine their long-term success. To learn more about specific cost-cutting strategies and navigating tariff uncertainty, explore resources on effective business model development and resilient supply chain management. Understanding the complexities of U.S. companies slashing costs amid tariff uncertainty is crucial for navigating the current economic landscape.
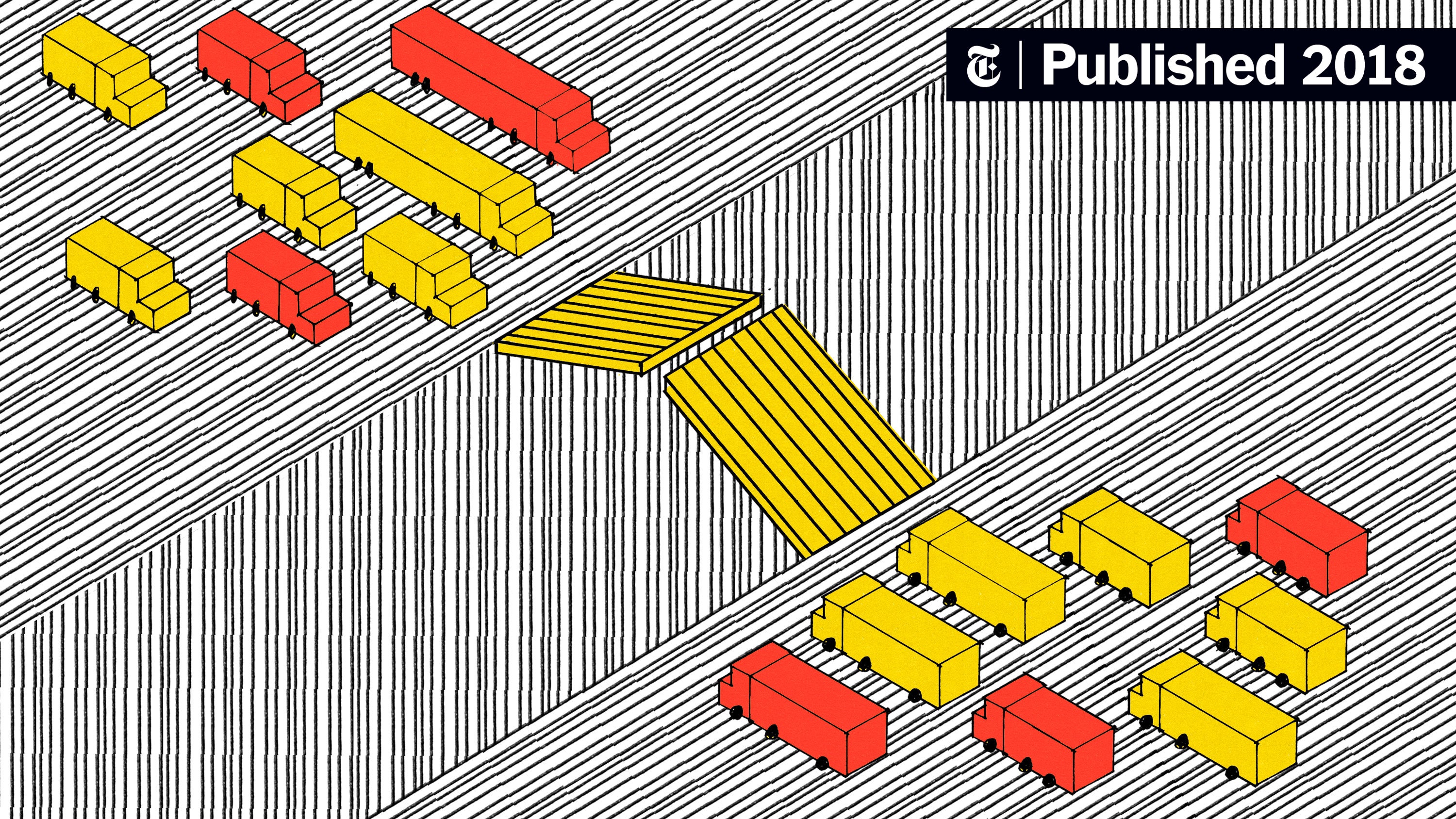
Featured Posts
-
Fox News Faces Defamation Lawsuit From January 6th Figure Ray Epps
Apr 29, 2025 -
Ecb Lingering Pandemic Fiscal Support Fuels Inflation
Apr 29, 2025 -
Turbulenzen In Der Bundesliga Lask Schwaechelt Klagenfurt Droht Der Abstieg
Apr 29, 2025 -
Hong Kong Share Sale Greenlit For Hengrui Pharma
Apr 29, 2025 -
The Porsche Paradox International Love Vs Australian Reception
Apr 29, 2025