The Big Rig ROCK Report 3.12 And Its Implications For Rock 101
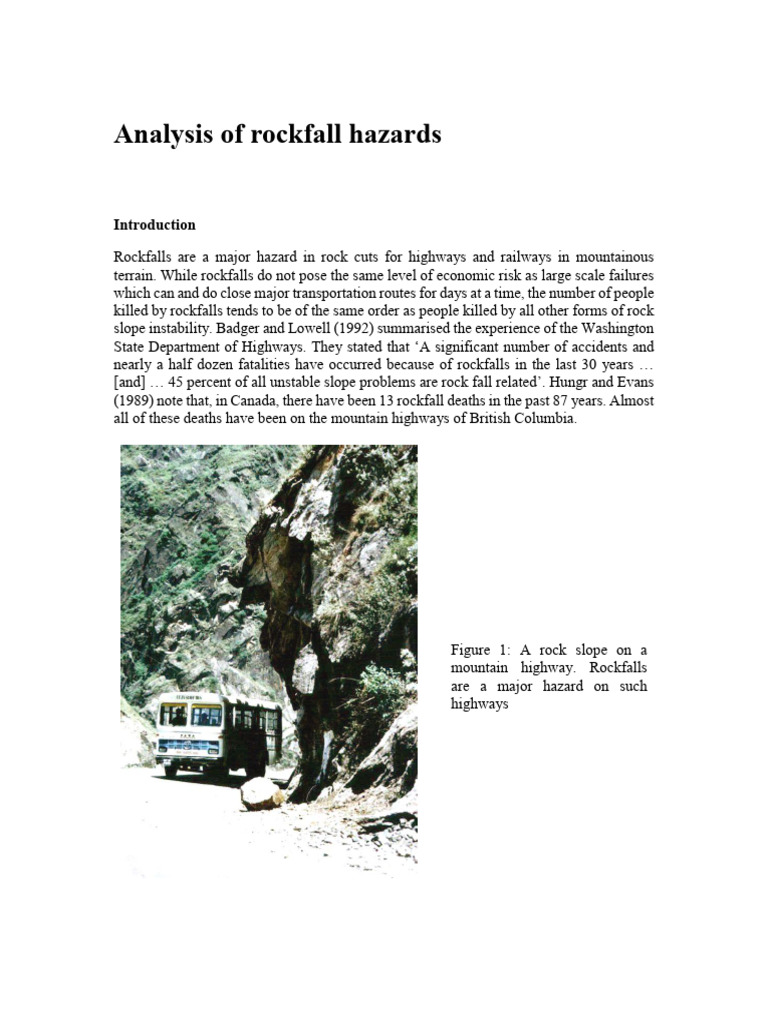
Table of Contents
Key Findings of the Big Rig ROCK Report 3.12
The Big Rig ROCK Report 3.12 presents a detailed overview of current practices within Rock 101, highlighting both strengths and areas needing improvement. The report's findings are categorized into several key areas, summarized below.
Safety Concerns Highlighted in the Report
The report underscores several significant safety concerns impacting Rock 101. These include:
- Increased Accident Rates: A notable increase in accidents related to [Specific equipment or activity within Rock 101] has been observed, necessitating immediate attention to safety protocols.
- Equipment Malfunctions: The report identifies specific equipment malfunctions as a contributing factor to accidents, emphasizing the need for improved maintenance schedules and training on equipment operation.
- Inadequate Training: A deficiency in the current training provided to Rock 101 participants in terms of safety procedures and emergency response protocols is highlighted. This points to the necessity for enhanced safety training modules.
- Lack of Proper PPE: Insufficient use of Personal Protective Equipment (PPE) was cited as a significant contributing factor to injuries. Emphasis on PPE use and its importance is crucial.
These safety concerns require immediate action to mitigate risks and improve overall safety within Rock 101 operations. Effective risk mitigation strategies are crucial for preventing future incidents.
Efficiency Improvements Suggested by the Report
Beyond safety, the Big Rig ROCK Report 3.12 suggests several areas for efficiency gains within Rock 101:
- Technological Advancements: The report advocates for the integration of new technologies to streamline processes and improve productivity. Specific technologies mentioned include [mention specific technologies].
- Workflow Optimization: The report identifies opportunities to optimize workflows through better process mapping and task delegation, leading to significant efficiency improvements.
- Improved Resource Allocation: A more efficient allocation of resources – both human and material – is suggested to maximize productivity and minimize operational costs. This includes better scheduling and optimized resource management.
Implementing these suggestions can contribute significantly to operational excellence within Rock 101, leading to substantial productivity improvements and cost savings.
Regulatory Changes and Compliance
The Big Rig ROCK Report 3.12 also outlines the necessity for regulatory compliance and adherence to updated industry standards. This includes:
- New Compliance Requirements: The report specifies new regulatory requirements related to [Mention specific regulations] that Rock 101 participants must meet.
- Updated Industry Standards: The report suggests aligning Rock 101 practices with the latest industry standards to ensure compliance and best practices. This includes changes to operational standards and safety standards.
Staying abreast of and adhering to these regulatory changes is paramount to maintain legal compliance and avoid potential penalties. Regular updates on legal requirements are essential.
Implications for Rock 101 Training and Certification
The findings of the Big Rig ROCK Report 3.12 necessitate significant changes to Rock 101 training and certification.
Updating Curriculum to Reflect Report Findings
Rock 101 curriculum must be updated to reflect the report’s findings, focusing on:
- Enhanced Safety Training: The new curriculum must include comprehensive safety training modules that address the identified safety concerns, emphasizing accident prevention and risk mitigation. This requires a robust curriculum development process.
- Integration of New Technologies: Training on the newly recommended technologies must be incorporated into the curriculum to ensure participants can effectively utilize these tools for improved efficiency.
- Updated Regulatory Information: The curriculum must integrate the latest regulatory updates and compliance requirements outlined in the report.
These curriculum updates are crucial for ensuring that Rock 101 participants receive the most current and relevant training.
Impact on Certification Requirements
The report may necessitate changes to existing certification requirements, possibly leading to:
- Revised Competency Assessments: New competency assessments may be required to ensure participants demonstrate proficiency in the new safety procedures and the use of updated technologies.
- Refresher Courses: Refresher courses or continuing education programs may become necessary to update existing certifications and ensure continued competence.
- Increased Stringency: Certification requirements may become more stringent to reflect the heightened importance of safety and compliance.
These changes ensure that Rock 101 certifications remain relevant and reflect current best practices.
Addressing New Safety Procedures in Training
Integrating new safety procedures into Rock 101 training is crucial, including:
- Hazard Identification Training: Training should equip participants with the skills to identify and assess potential hazards in their work environment.
- Emergency Response Training: Participants need comprehensive training in emergency response protocols to handle various situations effectively.
- Regular Safety Audits: Regular safety audits and reviews will help to continuously monitor and improve safety practices.
This proactive approach to safety training is essential to creating a safer work environment for all involved in Rock 101.
Best Practices for Implementing Changes Based on the Big Rig ROCK Report 3.12
Implementing the changes suggested by the Big Rig ROCK Report 3.12 requires a strategic and phased approach.
Phased Implementation Strategies
A phased implementation strategy minimizes disruption and allows for continuous improvement:
- Prioritization of Critical Changes: Focus on implementing the most critical changes first, addressing immediate safety concerns and regulatory compliance requirements.
- Pilot Programs: Conduct pilot programs to test the effectiveness of new training modules and procedures before widespread implementation.
- Gradual Rollout: Roll out changes gradually to avoid overwhelming the Rock 101 community and allow for effective feedback and adjustments.
This methodical approach ensures a smooth transition and allows for necessary adjustments based on feedback.
Resource Allocation and Support
Successful implementation requires appropriate resource allocation and support:
- Budget Allocation: Allocate sufficient budget for training materials, equipment upgrades, and technical support.
- Training Resources: Invest in comprehensive training materials and resources to support the updated curriculum.
- Technical Support: Provide adequate technical support to address any challenges during the implementation process.
Adequate resource allocation is key to successful change management.
Ongoing Monitoring and Evaluation
Continuous monitoring and evaluation are essential to ensure the long-term effectiveness of implemented changes:
- Performance Monitoring: Regularly monitor key performance indicators (KPIs) related to safety, efficiency, and compliance.
- Data Analysis: Analyze collected data to identify areas for further improvement and refine implementation strategies.
- Continuous Improvement: Embrace a culture of continuous improvement by regularly reviewing and updating procedures based on feedback and data analysis.
This cyclical process ensures that Rock 101 practices remain aligned with the evolving needs of the industry.
Conclusion: Moving Forward with the Big Rig ROCK Report 3.12 and Rock 101
The Big Rig ROCK Report 3.12 provides crucial insights into the current state of Rock 101, highlighting areas for improvement in safety, efficiency, and regulatory compliance. By proactively implementing the recommendations detailed in this report, the Rock 101 community can enhance safety, boost efficiency, and ensure continued success. Addressing the report's findings through curriculum updates, improved training, and a commitment to continuous improvement will strengthen Rock 101's position as a leading standard. Stay informed about future updates and actively participate in discussions about the future of Rock 101, contributing to a safer and more efficient industry. Let's work together to fully leverage the insights of the Big Rig ROCK Report 3.12.
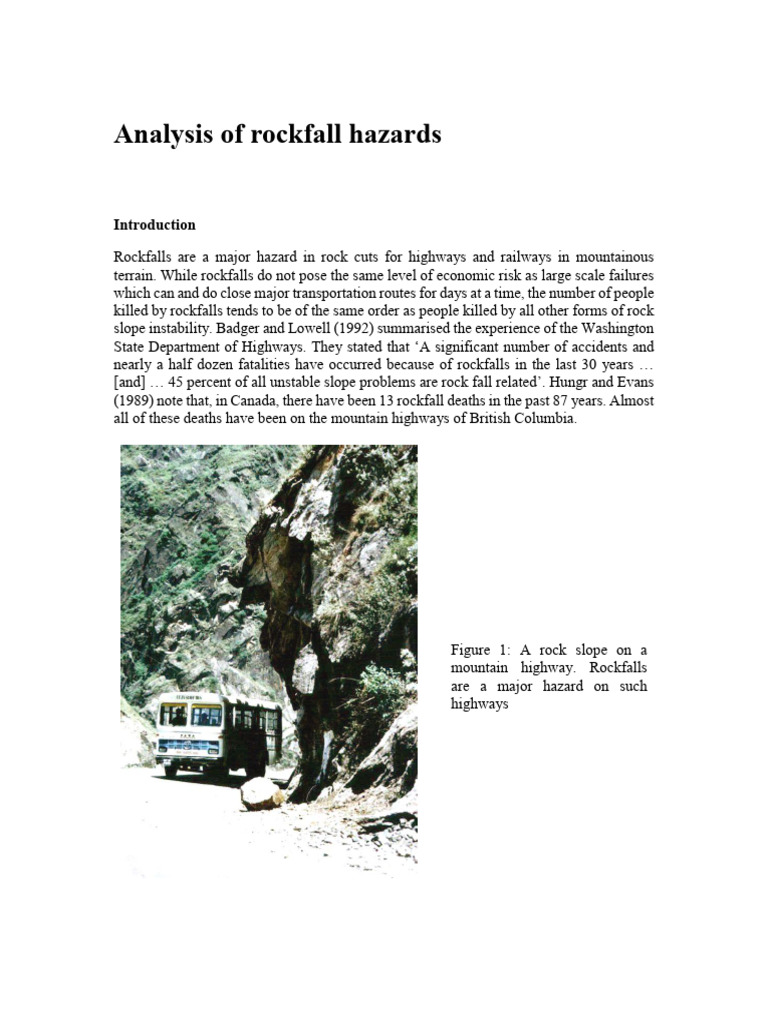
Featured Posts
-
Produce Hauling Truck Accident On I 83 Details Emerge
May 22, 2025 -
Google Searchs Ai Mode Opportunities And Implications
May 22, 2025 -
Googles New Approach Making Virtual Meetings More Tolerable
May 22, 2025 -
Peppa Pigs New Baby Gender Reveal Party
May 22, 2025 -
Succession Planning For The Ultra Wealthy A Growing Trend
May 22, 2025
Latest Posts
-
What Movies Are Leaving Hulu This Month A Full List
May 23, 2025 -
The Complete List Of Movies Leaving Hulu This Month
May 23, 2025 -
6 000 Cannes Tickets Inside The Black Market For Exclusive Film Screenings
May 23, 2025 -
Movies Leaving Hulu This Month Your Complete Guide
May 23, 2025 -
Cannes Black Market High Demand Tickets And The Price Of Pure Auteur Fuel
May 23, 2025